Future
Oltre design e produzione, Additive per le riparazioni
Il progetto META partito dal laboratorio di Bari, in partnership con il Politecnico, ha aperto a una serie di progressi a favore delle tecniche di riparazione e delle trasmissioni meccaniche.
Feb 2022
Riparare è meglio che buttar via o sostituire. È tipico dell’economia circolare, ad esempio, perché si riduce il numero di scarti o rifiuti, si dà nuova vita agli oggetti e infine si risparmiano risorse, energia, materiali e costi per sostituire un oggetto danneggiato con uno nuovo.
È attorno a tale concetto di sostenibilità e all’avanguardistica tecnologia additive (anche chiamata stampa 3D metallica), che ruota il progetto di ricerca META, sostenuto dalla Regione Puglia, coi suoi obiettivi: potenziare la progettazione di trasmissioni di potenza e accessori per motori aeronautici, e accrescere le competenze di riparazione o riconfigurazione di componenti, con geometria anche complessa e prodotti con materiali innovativi, difficili da realizzare e trattare mediante i tradizionali processi di produzione metallurgica.
“L’additive va ben oltre la capacità di disegnare geometrie complesse e ‘stampare’ parti di motore partendo da polvere metallica” spiega Manuela Perrone, Advanced Repair Technologies Leader e referente di Avio Aero per il progetto META. “Offre infatti la possibilità di recuperare costose parti motore usurate attraverso il ripristino della forma originaria o di incrementarne la vita utile con rivestimenti superficiali che persino esaltano le caratteristiche meccaniche grazie all’impiego di materiali altamente performanti.”
Una capacità tecnologica che, chi conosce le capacità di Avio Aero, potrà ricordare attraverso i nomi delle due tecniche di riparazione avanzate basate su tecnologie additive e nate all’interno del laboratorio congiunto di Avio Aero e Politecnico di Bari – l’ARDC, Apulia Repair Development Center: il Cold Spray e la Laser Deposition.
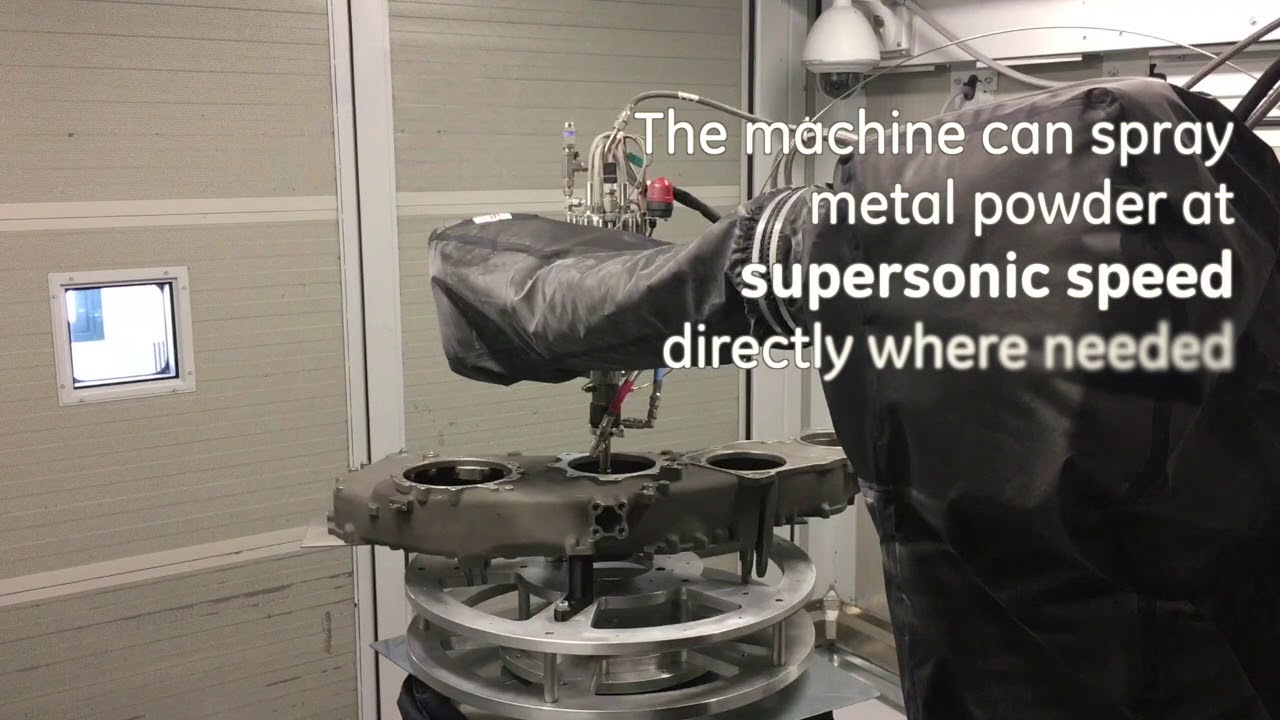
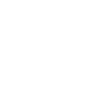
All’interno del campus universitario pugliese, l’ARDC ha lavorato senza sosta sin dall’inizio del progetto META, patrocinato anche da Governo e Unione Europea. “Non ci sono stati stop neppure durante la prima metà del 2020”, dice Perrone, “abbiamo condotto negli ultimi tre anni attività di standardizzazione e miglioramento dei processi organizzativi per irrobustire le metodologie di sviluppo di nuova tecnologia, mutuando inoltre da GE Aviation il metodo Repair Readiness Level (che facilita il lavoro tra funzioni aziendali in maniera integrata e consente di definire i vantaggi economici del repair e di accelerarne sviluppo e industrializzazione)”.
Già nel 2018, la tecnica di Cold Spray – che consente di spruzzare polvere metallica a velocità supersonica per ricostruire dettagli o ripristinare le dimensioni originali di una parte di motore aeronautico senza alterarne le proprietà fisico-meccaniche – aveva completato e reso disponibile la riparazione su diametri interni della trasmissione accessori del GE90.
Negli ultimi anni, sono stati completati sviluppo e processo di repair anche per gli adapter della trasmissione del GE90, componenti dalle geometrie particolarmente complesse, che includono nuove leghe in alluminio. Ed è in avanzata fase di sviluppo un repair su componente turbina (lega a base nichel), che permette un ulteriore importante salto tecnologico con l’impianto utilizzato quasi al massimo della sua capacità per velocità e pressione.
Per la tecnica di Laser Deposition – che invece permette di depositare polvere di metalli o leghe tramite laser – è stata sviluppata ed ottimizzata la capacità di ripristino dimensionale del profilo aerodinamico di pale di turbina LPT con lega base titanio allo stato grezzo: all’interno di META, sono state completate le prove su un componente reale, ottenendo sei pale turbina finite e conformi a disegno.

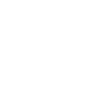
“Attraverso il progetto META abbiamo condotto ulteriori attività di ottimizzazione del repair, con l’obiettivo di semplificare il processo di deposizione e migliorare ulteriormente le proprietà meccaniche del deposito. Questo faciliterà il proseguo delle attività di sviluppo di analoghe operazioni di riparazione su pale turbina di motori in esercizio, come quelle del GEnx in TiAl per esempio” dice Perrone.
La portata dell’innovazione tecnologica è talmente ampia che ha coinvolto, insieme al Politecnico di Bari sede del laboratorio in partnership con Avio Aero e alla corregionale Università del Salento (entrambe nella rete europea E-TDCs di collaborazione per il futuro del volo), anche i team GE di ingegneria in USA e di Bangalore che hanno contribuito come agenti esterni del progetto con la loro capacità e conoscenza. Di recente, la rete E-TDC si è ulteriormente ampliata coinvolgendo anche ATLA – specializzata nella produzione e riparazione di componenti di turbine a gas – che ha disponibili processi per supportare la sperimentazione su parti reali e ha avviato linee di ricerca complementari.
Un altro importante aspetto, non affatto trascurabile, è che le attività sperimentali relative al progetto META hanno permesso a diversi talenti del Politecnico di Bari di distinguersi nella progettazione delle attività sperimentali, come nella sperimentazione vera e propria sugli impianti e per la valutazione dei risultati delle prove sperimentali.
“I ricercatori e i professori del PoliBa hanno guidato gli assegnisti nel loro lavoro quotidiano e condiviso con noi idee ed esperienze, in un lavoro di squadra che si è dimostrato efficace e proficuo”, conclude Perrone che ha lavorato fianco a fianco con Sabina Luisa Campanelli. Professore Associato nel settore "Tecnologie e Sistemi di Lavorazione" presso il Dipartimento di Meccanica, Matematica e Management del Politecnico di Bari, Sabelli ha guidato, insieme al Professor Ludovico, le attività di ricerca sui processi di riparazione con tecnologia additive.
"I ricercatori e i professori del PoliBa hanno guidato gli assegnisti nel loro lavoro quotidiano e condiviso con noi idee ed esperienze, in un lavoro di squadra che si è dimostrato efficace e proficuo"
“La nostra collaborazione con Avio Aero era già partita in precedenza col Progetto PON TEMA, per poi sfociare nella nascita del Laboratorio ARDC”, ricorda la Prof. Campanelli. “Per noi, il valore aggiunto della collaborazione è stato un notevole incremento del know-how su tecnologie innovative e all'avanguardia per motori aeronautici e alla formazione di giovani neolaureati che hanno la possibilità di acquisire esperienza in un laboratorio congiunto fra azienda ed università. Inoltre, all’interno di META, abbiamo contribuito allo sviluppo del primo processo di riparazione al mondo su componenti di motori aeronautici realizzato mediante tecnologia Cold Spray.”
Infine, la ricerca dedicata a sviluppo e progettazione di trasmissioni meccaniche - ovvero la trasmissione di potenza (Power Gear Box, PGB) e quella accessori (Accessory Gear Box, AGB) - che nella fattispecie ha interessato il nuovo motore turboelica Catalyst. La prima assolve la funzione di fornire potenza all’elica, la seconda invece fornisce energia al motore e all’aereo stesso oltre a integrare il serbatoio olio.
“Sono entrambi prodotti che richiedono parametri di qualità molto alti, finalizzati a massimizzarne l’affidabilità e dunque a evitare malfunzionamenti che impattano sull’intero motore” spiega Paolo Di Maggio, Mechanical Component Design Manager di Avio Aero. “La PGB, nello specifico, è stata disegnata e realizzata tramite additive manufacturing, beneficiando così nel peso e nel numero di parti assemblate. Il percorso di progettazione e validazione è stato sfidante, infatti è la prima volta nella storia dell’aeronautica che un componente tanto cruciale viene realizzato con stampa 3D. Per questo, i banchi prova hanno svolto un ruolo chiave nella validazione della PGB (testando e verificando la risposta dinamica) come anche dell’AGB”.
“Per questa parte del progetto abbiamo portato avanti una intensa attività di concurrent engineering con i Test Engineer del nostro centro del Sangone (Torino) e persino coi colleghi di GE Aviation Turboprop a Praga, per l’esecuzione di test motore reali. Infatti, i progettisti dei banchi prova sono entrati a far parte nell’ampio team del nuovo GE Catalyst, per garantire l’integrazione ed il corretto trasferimento delle informazioni relative ai moduli da sottoporre alle prove” aggiunge Giorgio Giaffreda, Test Rig Design Manager di Avio Aero.
Sperimentazioni e apprendimenti maturati all’interno del progetto META - specie riguardanti le attività di progettazione di banchi prova per vere trasmissioni di potenza e comando accessori - sono stati cruciali per permettere ad Avio Aero di investire sul centro sperimentale del Sangone dove otto nuovi banchi prova per trasmissioni sono stati costruiti dal 2017 al 2019.