Invent
No smoking guns
La prima riparazione con innovative tecniche additive è già realtà ed è stata eseguita in un Campus universitario grazie a una pistola speciale.
Sep 2017
Le esigenze primarie degli operatori del cielo, relativamente ai motori aerei in servizio, possono essere fondamentalmente sintetizzate in due parole: efficienza e affidabilità. Quello che Avio Aero sta mettendo in pratica per il service, attraverso le sue Repair Station (officine e stabilimenti autorizzati per il service) e i suoi laboratori e centri di ricerca, è un sistema associabile al concetto di ‘cervello e braccia’. Il fine ultimo è massimizzare efficienza e affidabilità dei servizi di riparazione e manutenzioni offerti. All’interno di questo sistema, emerge il lavoro di ricerca e sviluppo che sta conducendo il ‘cervello’, ovvero l’Apulia Repair Development Center che iniziò la sua attività alla fine del 2016. Qui, all’interno del campus del Politecnico di Bari, sono cominciate le prime vere attività di repair con tecniche additive (ovvero con aggiunta di metallo tramite tecnologie speciali) su reali componenti di motori aeronautici. Attività e processi che una volta sviluppati e certificati saranno pronti per essere adottati nelle officine - le ‘braccia’ - di Brindisi o Pomigliano.
Il laboratorio di Bari, nato da una Partnership con il Politecnico pugliese, si estende su 3200mq, in sale impianti e open space che somigliano ai tipici ambienti di lavoro in cui ingegneri di differenti età, percorsi accademici e provenienze, sia geografiche sia professionali, lavorano fianco a fianco progettando e studiando non soltanto tecniche di riparazione con metodi additive. Qui infatti si trovano gli ingegneri di GE Aviation e Avio Aero che lavorano ai programmi del futuro come l’ATP (da Marzo 2018 ufficialmente presentato con il nome GE Catalyst), sviluppano sistemi elettrici per la propulsione o per il controllo del motore (appartenenti a un altro laboratorio, Energy Factory Bari). Sono affiancati sia da ricercatori che da professori del Politecnico e si intrecciano con la trama mondiale dei Global Research Center di GE, poiché la conoscenza e la sperimentazione raggiungono il massimo potenziale se condivisi.
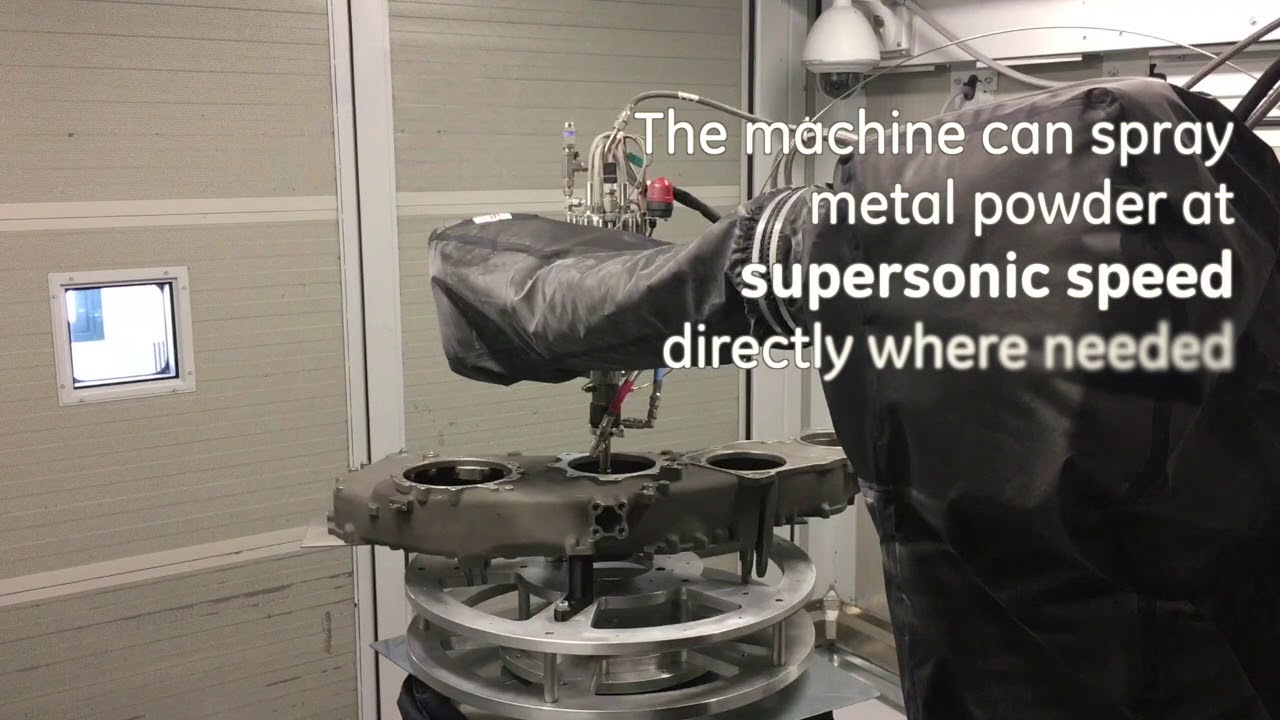
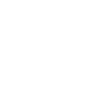
Ma è solo l’Apulia Repair Development Center che, all’interno del campus, può operare su due macchine a tecnologia additive ospitate da una grande sala del complesso: Cold Spray e Laser Deposition. Grazie a queste due macchine, ricerca e design possono prendere forma reale e permettere uno studio empirico. L’essenza delle due tecnologie, infatti, non tradisce le tipiche promesse dell’additive: gestione efficiente della complessità geometrica e reverse engineering. Ovvero, il poter passare dallo schermo alla costruzione fisica tramite un processo che aggiunge materiale metallico in polvere su un componente, strato su strato.
La base di partenza è la medesima dunque, con a sola eccezione che qui non si parte da un disegno CAD (coputer-aided design) da stampare in 3D con le tecniche EBM o di laser melting, ma si scansiona o digitalizza una parte reale di un motore aereo che va riparata o ricostruita. Proprio in questo mese e in concreto, la tecnologia Cold Spray sviluppata a Bari ha stabilito un primato: per la prima volta è stata applicata ad un componente GE Aviation. Nella fattispecie, al case della trasmissione accessori del mitico GE90 che motorizza l’aeroplano a lungo raggio Boeing 777.
Quello che fa il Cold Spray è estremamente affascinante dal punto di vista della fisica: l’impianto è costituito da una camera di circa 4,5x4,5 mt, al centro una pistola che funziona con gas (azoto o elio) e capace di spruzzare polvere metallica a velocità supersonica su un pezzo che si trova installato sulla piastra centrale dell’impianto. “Ogni singola particella di metallo proveniente dalla pistola, caricata con polvere, si attacca alla parte (o porzione) di componente da ricostruire o riparare per effetto cinetico, la pistola opera a freddo a differenza di tecnologie additive che agiscono attraverso il fascio di laser o di elettroni generando calore. Questo permette un altro importante beneficio, le proprietà fisico-meccaniche del pezzo su cui agiamo non subiscono alterazioni, e il processo di fusione metallica risulta ugualmente perfetto” racconta Giulio Longo che al laboratorio di Bari coordina tutte le attività sui due impianti.
I componenti di motori aeronautici oggetto di queste attività di sviluppo per la riparazione apparterranno, dopo il GE90, anche a programmi come GEnx, CF6-80, CFM56, LM2500 e ad altri programmi di terze parti. In questo modo si otterrà la più vasta e variegata esperienza per parti di motori civili montate sugli aerei che usiamo ad esempio per viaggi domestici o intercontinentali. I componenti in questione sono casing, appunto, ma anche housing (involucri delle trasmissioni di potenza o accessori) e serbatoi, fino ad arrivare a ingranaggi e altre parti dal design tipicamente complesso. E i metalli, o meglio le leghe più comunemente usate in aeronautica, la cui polvere può essere applicata con tali tecnologie sono diversi: acciaio, alluminio, magnesio e titanio…leghe che ovviamente comprendono la più celebre nel settore, il TiAL (titanio allumino) usato per le pale del nuovissimo motore GE9X.
Particolarmente indicata per il TiAl è infatti l’altra tecnologia presente all’Apulia Repair Development Center: la Laser Deposition, che è ancora in fase di test e vedrà a brevissimo la sua applicazione su vere parti di un motore. In questo caso la polvere viene depositata sul pezzo da riparare o nella porzione da ricostruire tramite un laser ad altissima precisione. La Laser Deposition è indicata per i componenti molto sottili o di piccole dimensioni, difficili da saldare o recuperare: è il caso di pale turbina o degli statori, parti rotanti.
Non è da sottovalutare, infine, un aspetto incredibilmente importante della tecnologia additiva, che inoltre la distingue dal punto di vista ecologico oltre ad arrecare vantaggi per il cliente, ovvero la possibilità di sostituire e riparare parti evitando costi per parti nuove e limitando il consumo di materiali. La polvere non va sprecata (poiché quella in esubero viene raccolta e riutilizzata, come in ogni tipico processo additive) e il processo quanto a emissioni e rumore è infinitamente più conveniente dei processi tradizionali.