Future
Additive for repairs: beyond design and manufacturing
In partnership with Politecnico, the META project that began in the Bari laboratory, has opened up a series of advances for repair techniques and mechanical transmissions.
Feb 2022
Repair is better than throwing away or replacing. Experts of the circular economy, for instances, know this well. The number of discarded items or waste is reduced, objects are given a new life, and resources, energy, materials and costs are saved when replacing a damaged part with a new one.
It is around this concept of sustainability and cutting-edge additive technology (also called 3D metal printing) that the META research project revolves, with the support of the Apulia Region. It has the following objectives: to enhance the design of power transmissions and accessories for aircraft engines and to increase the repair skills or components’ reconfiguration, even with complex geometry and produced with innovative materials that are difficult to make and treat through traditional metallurgical production processes.
"Additive goes far beyond the ability to design complex geometries and 'print' engine parts from metal powder," explains Manuela Perrone, Advanced Repair Technologies Leader and the Avio Aero contact for the META project. "It offers the possibility of recovering expensive worn engine parts by restoring their original shape or increasing their useful life with surface coatings that even enhance their mechanical characteristics through the use of high-performance materials."
Those who know Avio Aero's capabilities will remember this technological capacity through the names of the two advanced repair techniques, based on additive technologies from within the joint laboratory of Avio Aero and Politecnico di Bari- ARDC, Apulia Repair Development Center: Cold Spray and Laser Deposition.
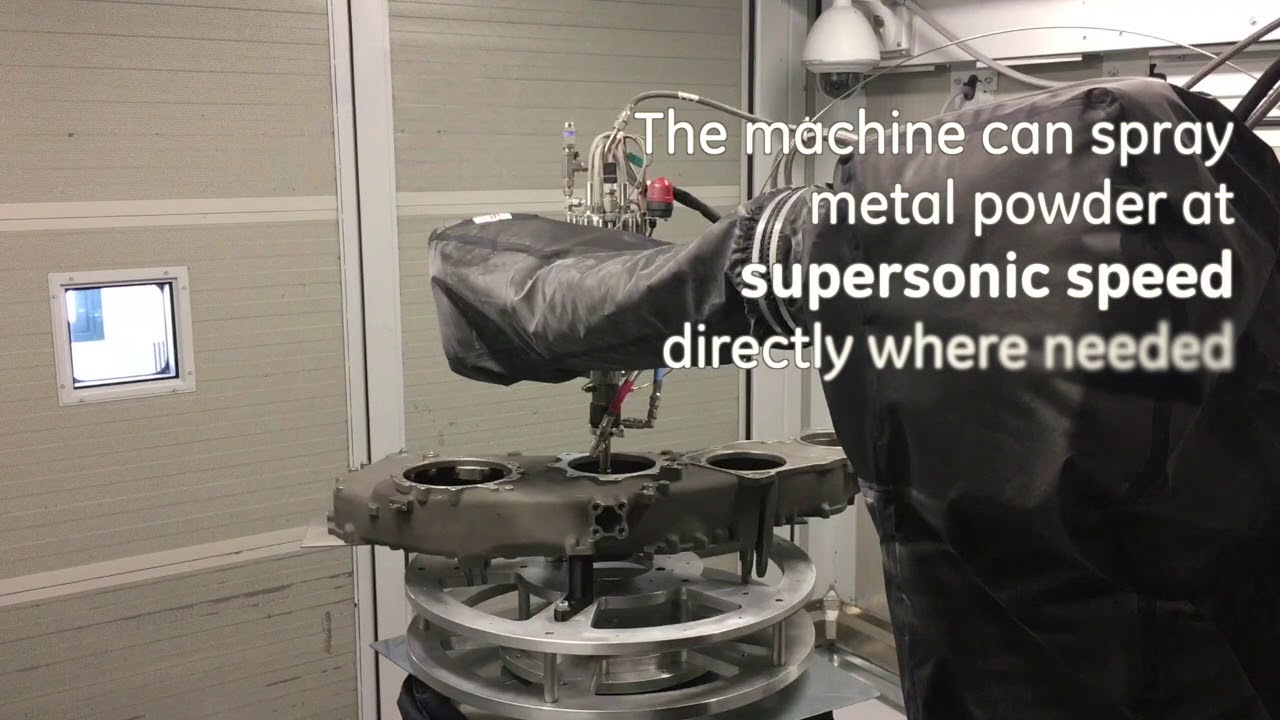
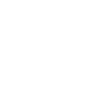
Within the Apulian university campus, ARDC has been working non-stop since the beginning of the META project, also sponsored by the Government and the European Union. "There has been no pause, not even during the first half of 2020," says Perrone. "Over the last three years, we have conducted standardization and improvement of organizational processes to strengthen the methodologies of new technology development. We borrowed the Repair Readiness Level method from GE Aviation (which facilitates the work between business functions in an integrated manner, allows the economic advantages of repair to be defined, and its development and industrialization accelerated)."
Already in 2018, the Cold Spray technique - which consists of spraying metal powder at supersonic speeds to reconstruct details or restore the original dimensions of an aircraft engine part without altering its physical-mechanical properties - completed and made the repair possible on internal diameters of the GE90 accessory drive.
In recent years, development and repair processes have also been completed for the GE90's transmission adapters, components with particularly complex geometries that include new aluminum alloys. And a repair on a turbine component (nickel-based alloy) is in an advanced stage of development, which allows a further significant technological jump with the system used almost at its maximum capacity in terms of speed and pressure.
The Laser Deposition technique - which allows metal or alloy powder to be deposited by laser - has been developed and optimized for the ability to restore the size of the LPT turbine blade airfoil with raw-state titanium-based alloy. Within META, tests have been completed on an actual component, obtaining six finished turbine blades that conform to the drawing.

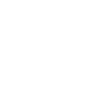
"Within the META project, we conducted additional repair optimization activities to simplify the deposition process and further improve the mechanical properties of the deposited material. This will facilitate the continuation of development activities for similar repair operations on turbine blades of operating engines, such as those of the GEnx in TiAl, for example," says Perrone.
The scope of technological innovation is so extensive that it has involved, along with Politecnico di Bari (the location of the laboratory in partnership with Avio Aero) also, in the same region, the University of Salento (both in the European E-TDCs network collaboration for the future of flight), as well as GE engineering teams in the USA and Bangalore that have contributed to the project as external agents, with their skills and knowledge. Recently, the E-TDC network has been further expanded to include ATLA - specializing in the manufacture and repair of gas turbine components - that has processes available to support testing on actual parts and initiated complementary lines of research.
Another critical aspect is that the experimental activities related to the META project have allowed Politecnico di Bari’s talents in the design of testing activities to be recognized. This includes the actual experiment on the systems and the assessment of the experimental tests’ results.
“Researchers and professors from Politecnico di Bari guided the fellows in their daily work and shared ideas and experiences with us, in teamwork that proved effective and fruitful," concludes Perrone, who worked side by side with Sabina Luisa Campanelli: an Associate Professor in the field of "Technologies and Processing Systems" in the Department of Mechanics, Mathematics and Management of the Politecnico di Bari, along with Professor Ludovico, Prof. Campanelli led the research on repair processes with additive technology.
"Researchers and professors from Politecnico di Bari guided the fellows in their daily work and shared ideas and experiences with us, in teamwork that proved effective and fruitful"
"Our collaboration with Avio Aero had already started earlier with the PON TEMA Project and resulted in the birth of the ARDC Laboratory," recalls Prof. Campanelli. "For us, the added value of the collaboration was a significant increase in know-how on innovative, cutting-edge technologies for aircraft engines and the training of young graduates, who have the opportunity to gain experience in a joint laboratory between the company and the university. In addition, within META, we helped develop the world's first repair process on aircraft engine components using Cold Spray technology."
Finally, research dedicated to the development and design of mechanical transmissions - i.e., power transmission (Power Gear Box, PGB) and accessory transmission (Accessory Gear Box, AGB) - that in this case involved the new Catalyst turboprop engine. The first supplies power to the propeller, while the second supplies energy to the engine and the aircraft itself, and integrates the oil tank.
"These are both products that require very high-quality parameters, aimed at maximizing reliability and therefore avoiding malfunctions that impact on the entire engine," explains Paolo Di Maggio, Mechanical Component Design Manager at Avio Aero. "Specifically, the PGB was designed and manufactured by Avio Aero using additive manufacturing, benefiting in terms of weight and number of assembled parts. The design and validation process was challenging, and it is the first time in the history of aeronautics that such a crucial component has been 3D printed. Test stands played a key role in validating the PGB (to test and verify dynamic response) as well as the AGB."
"For this part of the project, we carried out intensive concurrent engineering activities with the Test Engineers from our Sangone center and even with colleagues from GE Aviation Turboprop in Prague to perform real engine tests. The test rig designers have become part of the new GE Catalyst’s extensive team, guaranteeing the integration and the correct transfer of the information related to the modules to be tested," adds Giorgio Giaffreda, Test Rig Design Manager at Avio Aero.
The experiments and research acquired within the META project - regarding the test bench design for actual power transmissions and accessory drives - were crucial for Avio Aero's investment at the Sangone (Turin) test center, where about eight new test benches for transmissions were built from 2017 to 2019.