Invent
Magneto-odporny
W laboratoriach Avio Aero przeprowadzane są testy elektromagnetyczn, których celem jest zapewnienie, że żadne pole zewnętrzne nie zmieni wydajności silnika.
Apr 2019
Majestatyczna, elegancka i skomplikowana konstrukcja silnika samolotu niezmiennie budzi podziw. Kiedy na niego spojrzymy, dostrzegamy kształt, rozmiar, tysiące rur, które prowadzą do metalicznego serca. Często jednak zapominamy, że silnik, zanim zostanie zainstalowany pod skrzydłem samolotu, stanowi swoisty rezultat projektu, pomysłu. Silnik samolotu ożywa na długo przed tym, zanim przybierze ostateczny swój kształt. Długo „żyje” w fazie projektowania i dojrzewania, co pozwala w pełni zaspokoić potrzeby klienta końcowego.
Kluczową rolę w tej fazie odgrywają badania laboratoryjne przeprowadzane na różnych elementach silnika. „W Avio Aero istnieje wiele laboratoriów, które służą zasadniczo do testowania i walidacji komponentów silników lotniczych z mechanicznego punktu widzenia, ale także pod względem elektromagnetycznym, wibracyjnym, termoklimatycznym, metrologicznym i wieloma innymi” - wyjaśnia Maurizio Saroglia, Kierownik Laboratoriów i Inżynierii Jakości CA&M (Controls & Accessories Marine).
W laboratorium Rivalta koło Turynu spotkaliśmy się z Davide Ronchetto, specjalistą zajmującym się elektroniką silnika Catalyst: to nowy silnik turbośmigłowy GE, stworzony w Europie. „W ramach programu GE Catalyst działam jako Lider Układu Elektrycznego Silnika, co oznacza, że koordynuję i jestem kontaktem technicznym podczas procesu rozwoju całego systemu elektrycznego silnika. Układ elektryczny wykonuje aktywną kontrolę mocy wytwarzanej przez silnik oraz monitoruje szereg parametrów krytycznych dla bezpiecznego i niezawodnego zarządzania jego eksploatacją.”
Ten wyjątkowy produkt na rynku silników turbośmigłowych, poprzez złożony system okablowania jest podłączony elektrycznie do czujników, w tym do czujników temperatury, ciśnienia, prędkości i momentu obrotowego. Jednocześnie zawiera również siłowniki, które są urządzeniami elektrohydraulicznymi, elektropneumatycznymi lub elektromechanicznymi, zdolnymi do przekształcania impulsów elektrycznych w ruch mechaniczny. Siłowniki umożliwiają zmienną geometrię (np. ruchome części komponentów, takie jak łopatki sprężarki), a także paliwo, skok śmigła i wiele więcej poza układem zapłonu silnika i małym generatorem elektrycznym, który służy do zasilania FADEC po uruchomieniu silnika. FADEC komunikuje się również z samolotem i przekazuje pilotowi ważne dane oraz odbiera informacje o działaniu samolotu.
"Nasze działania mają kluczowe znaczenie: układ elektryczny - zwłaszcza w silnikach najnowszej generacji - jest prawdziwym sercem silnika. Jest to element, który łączy wszystkie części i pozwala na bezpieczny lot"
Davide to osoba wyznaczona do kontaktów w Avio Aero w zakresie wszystkich tych działań, które pozwalają silnikowi „komunikować się”, wysyłać i odbierać sygnały oraz informacje z całego silnika w centrum kontrolonym. Ale przede wszystkim jest także punktem odniesienia dla certyfikacji całego systemu. „Wszystkie używane przez nas komponenty są zwykle certyfikowane przez dostawców surowców i półproduktów, którzy je wytwarzają. Jednak, aby kwalifikowały się do ich użycia w samolocie, muszą przejść szereg testów – których przeprowadzenie leży po naszej stronie – wykonywanych w kompletnym systemie elektrycznym.
Są to EMC - kompatybilność elektromagnetyczna (lub EMI, Zakłócenia Elektromagnetyczne), za pomocą których upewniamy się, że układ elektryczny silnika wykonuje dobrze swoją pracę w „brudnym” środowisku elektromagnetycznym, tj. nie jest izolowany ani chroniony przed zakłóceniami, bez żadnego negatywnego „wpływu”, który mógłby pogorszyć jego działanie; co z kolei pozwala stwierdzić, że silnik będzie działał bez zakłóceń w innym sprzęcie.
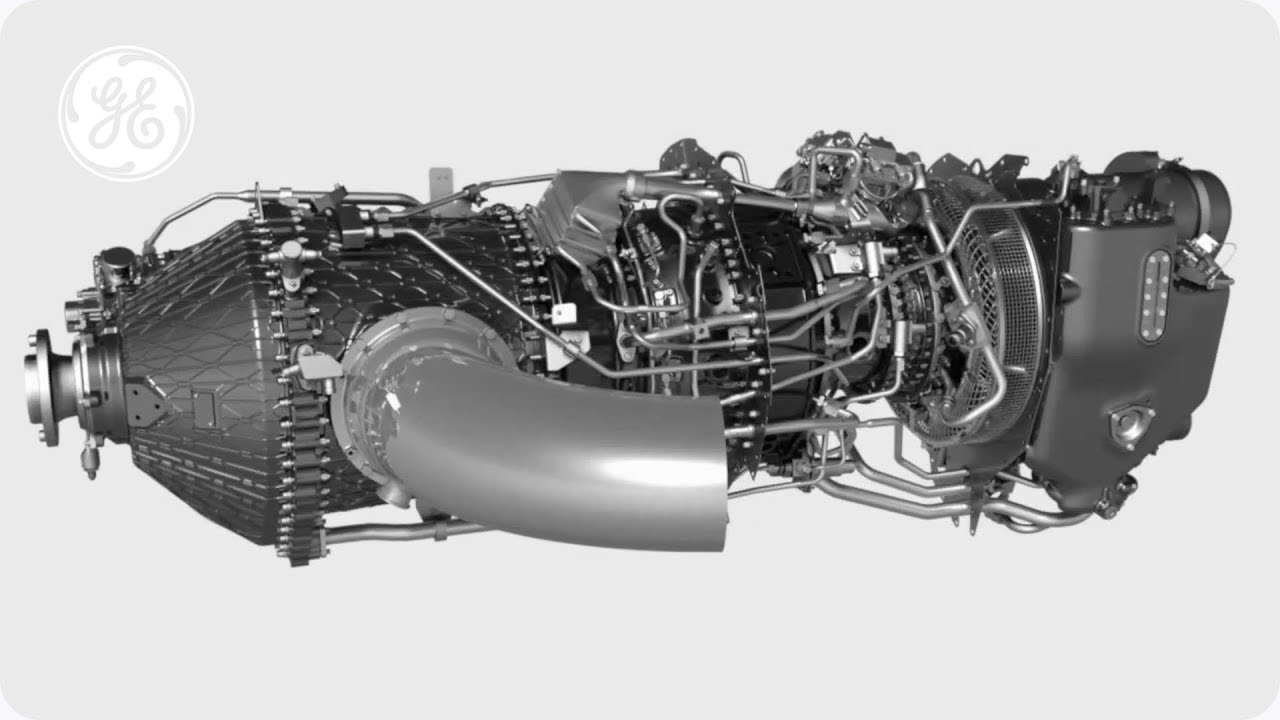
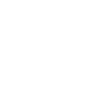
Wiele testów, które wykonujemy, należy przeprowadzać w komorach bezechowych, chronionych przed zewnętrznymi polami magnetycznymi, które mogłyby mieć negatywny wpływ na wynik testu. „Dysponujemy takimi komorami bezechowymi w Rivalta, co pozwala nam wykonywać dużą część badań wymaganych przez przepisy lotnicze.”
„Po wykonaniu tych operacji” - opowiada Ronchetto - „ustawiliśmy cały układ silnika elektrycznego w pomieszczeniu testowym lub komorze bezechowej, w tym sprzęt, który służy do stymulacji czujników, tak jakby działały one w silniku i przekazywały informacje do kokpitu samolotu. Dzięki testowi, uzyskujemy wszystkie dane przetwarzane przez EECU, a następnie analizujemy je w celu sprawdzenia, czy wystąpiły znaczące zakłócenia. Zakłócenia, w żargonie ekspertów, to wszystko to, co może wpływać na silnik w locie : na przykład sygnał radarowy lotniska lub innego samolotu, który zakłóca środowisko otaczające go polem elektromagnetycznym.
Jak zatem testuje się zakłócenia magnetyczne? Testy wykorzystują metodę otwartej pętli: ponieważ „prawdziwy” silnik nie jest dostępny - wysyłanie stałych poleceń z EECU (takich jak sterowanie siłownikiem) jest symulowane przez ustawienie stymulatorów czujnika w określonym punkcie. W tym momencie, zakłócenia testowe są rejestrowane i - jeśli zarejestrowane dane przekraczają ustalone limity – podlegają one analizie przeprowadzanej przez naszych kolegów w Centrum Kontrolnym w modelu symulacyjnym silnika w celu ustalenia, czy takie zaburzenie może mieć wpływ na ostateczne zachowanie silnika.
Inny test symuluje na przykład efekt uderzenia pioruna. Ponownie, należy sprawdzić, czy nic nie ulegnie awarii oraz czy nie pojawią się znaczne zakłócenia w pokładowym systemie elektrycznym. “Nasze działania mają kluczowe znaczenie: układ elektryczny - zwłaszcza w silnikach najnowszej generacji - jest prawdziwym sercem silnika. Jest to element, który łączy wszystkie części i pozwala na całkowicie bezpieczny lot” -podsumowuje Ronchetto.
To, co mogłoby jeszcze zaskoczyć podczas testów to pojawienie się takiego superbohatera jako Magneto albo może działanie sił takich, jak pioruny na Jowiszu. A może i to już nikogo nie zadziwi?