Invent
La fabbrica del futuro
Uno sguardo all’interno della fabbrica in cui le parti dei motori aerei vengono stampate in 3D.
Oct 2017
Situata sulle sponde della fertile pianura attraversata dal fiume Po, nel nord dell’Italia, la cittadina di Cameri potrebbe facilmente essere confusa con un tranquillo comune rurale. Ma percorrendo le strade circondate dai verdi campi fuori del paese, si può individuare un sorprendente contrasto.
Cameri, 11mila abitanti, è sede dell’unico sito di assemblaggio esterno agli Stati Uniti per il caccia F-35 Joint Strike Fighter di Lockheed Martin, il super jet che può decollare e atterrare in verticale. E proprio oltrepassando l’autostrada che costeggia questo stabilimento, si può trovare un’altra futuristica perla industriale: la fabbrica di stampa 3D di Avio Aero, che produce le lucenti pale turbina per il motore GE9X, il motore civile più grande al mondo, che GE Aviation sta sviluppando per la nuova generazione di aeroplani Boeing 777X. All’interno di un motore aereo le pale arrivano a 2500 giri per minuto, soggette al calore e altre incredibili fatiche fisiche. “Queste sono pale piuttosto grandi”, dice Giorgio Abrate, Engineering General Manager di Avio Aero. “Conduciamo moltissimi esperimenti per ottimizzare il lavoro su queste parti nel modo migliore”.
Un moderno edificio di acciaio e cristallo cromato di blu e grigio, lo stabilimento di Cameri ospita circa 20 macchine di stampa 3D della Arcam, grandi come degli armadi. Una sola di queste macchine è in grado di stampare fino a sei pale alla volta, lunghe 40 centimetri, direttamente da un disegno CAD sul computer attraverso un potente fascio di elettroni da 3 kilowatt. Il fascio di elettroni crea la pala dal basso fondendo insieme finissimi strati di alluminuro di titanio, uno sull’altro.
I progettisti di motori aerei adorano questo incredibile materiale, resistente anche al caldo, che pesa la metà delle leghe comunemente usate in aviazione, ma che è anche molto friabile. Fino all’avvento della stampa 3D, infatti, si usava un processo di stampaggio tramite forma che richiedeva strumenti costosi. “Questa fabbrica ci ha dimostrato l’arte di ciò che l’additive manufacturing rende possibile”, ha detto David Joyce, Presidente e AD di GE Aviation.
Il business di Joyce acquisì Avio Aero nel 2013. E nello scorso autunno GE ha anche acquisito il controllo azionario di Arcam, lanciando GE Additive, la nuova divisione concentrata sulle tecnologie di additive manufacturing e stampa 3D. L’additive è un’industria ancora molto giovane, sebbene attualmente sia in una fase di crescente sviluppo. Il capo di GE Additive, Mohammad Ehteshami, prevede una crescita che dai 7 miliardi di oggi, possa arrivare a 80 miliardi di dollari in dieci anni.
Avio Aero iniziò il suo viaggio nella stampa 3D più di un decennio fa. A quel tempo girava voce che GE aveva usato l’alluminuro di titanio, conosciuto come TiAl, per la primissima volta sul motore GEnx progettato per il Boeing 787 Dreamliner. “Per noi il passo avanti e l’investimento con questa tecnologia rappresentano qualcosa di molto importante”, dichiarò a FlightGlobal Robert Schafrik, al tempo Materials & Process Engineering General Manager di GE Aviation. “Dal momento che pesa la metà di una lega di nichel, c’è da credere che questo materiale verrà usato per molto altro tempo.”
Le pale che montavano su motori GE erano prodotte in fonderia. Ma Avio Aero, attirata dal nuovo mercato, scommise sulla stampa 3D. “Ci rendemmo conto di quanto era complesso produrre questo tipo di pale,” dice Abrate, “ma avemmo delle esperienze positive con la stampa 3D su un progetto militare”.
L’azienda italiana decise di sfruttare la vicinanza della linea di assemblaggio del Joint Strike Fighter e costruì lo stabilimento di additive manufacturing a Cameri. “La posizione geografica era parte della nostra strategia”, dice Abrate. “Lo stabilimento di Lockheed aveva aumentato la visibilità di quell’area tra le aziende dell’aerospazio. Volevamo promuovere la stampa 3D per nuovi potenziali clienti e quelli stavano tutti avvicinandosi alla zona.”
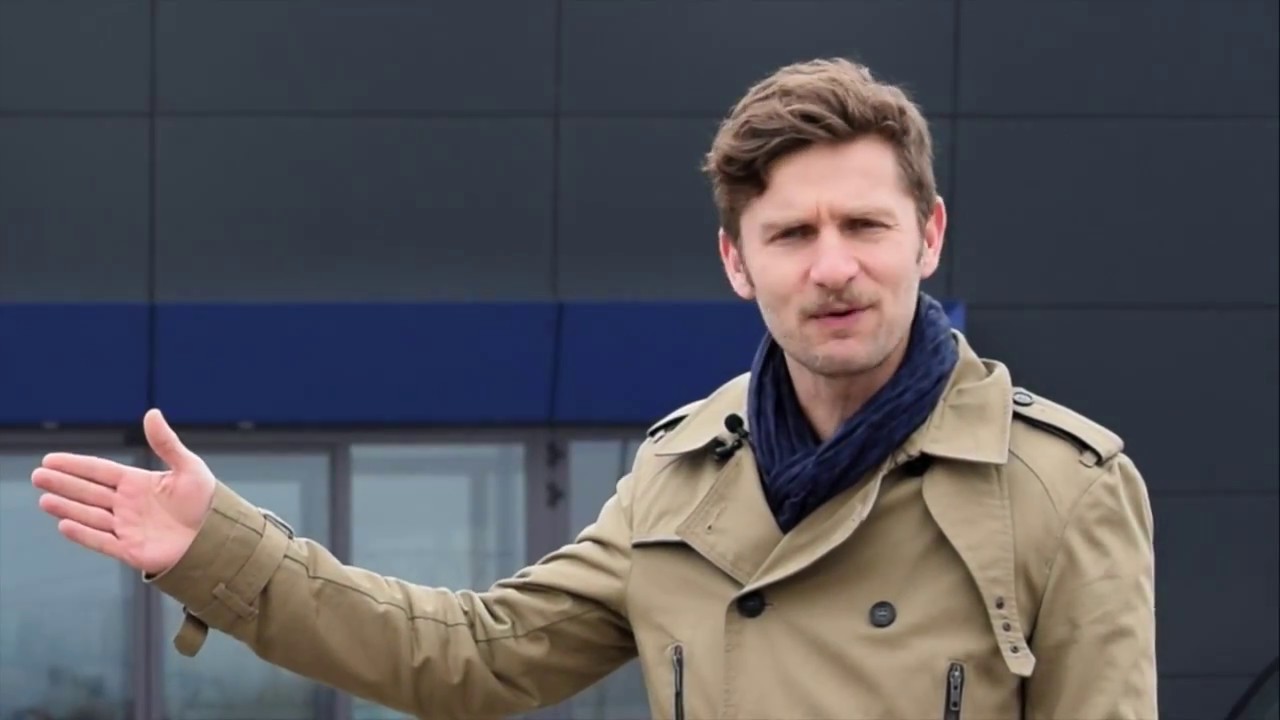
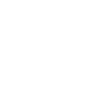
Quella scommessa aveva bisogno di stampanti 3D, che Avio Aero trovò nella ProtoCast, una pioneristica piccolo azienda italiana di stampa 3D che stava giusto nelle vicinanze. “Si trattava proprio di un garage” ricorda Abrate, “Lo chiamavamo ‘il sottomarino’ per via dello stretto spazio rimanente per il passaggio tra le macchine e le persone che vi lavoravano.”
Ma i primi tentativi con le machine laser ProtoCast furono fallimentari. Le pale si rompevano facilmente già quando Abrate e il suo team cercavano di staccarle dalla piattaforma sulla quale venivano stampate in 3D.
Tuttavia, il sottomarino ospitava un’arma segreta: una macchina Arcam che fondeva strati di polvere di TiAl attraverso un fascio di elettroni, con una potenza di molto superiore rispetto alle stampanti 3D che usavano il laser. Abrate cominciò a collaborare strettamente con Arcam al fine di aggiustare alcuni parametri delle macchine, rendere gli strati di polvere fusi più fini e accelerare il processo. Attraverso diversi esperimenti, Abrate scoprì anche dei vantaggi provenienti dal pre-riscaldamento della polvere prima di usare il fasci di elettroni: “a quel punto, capimmo cosa fare”.
Avio Aero acquistò ProtoCast e firmò un accordo in esclusiva con Arcam in modo da fornire le macchine con quelle modifiche che permettessero di stampare in TiAl. In cambio, Avio Aero promise ad Arcam l’acquisto di una serie di macchine.
Quando Avio Aero mostrò a GE cosa poteva fare con quella straordinaria lega, la multinazionale americana afferrò subito la grandezza dell’intuizione. GE Aviation stava giusto in quel periodo sviluppando il proprio programma di stampa 3D nei pressi del quartier generale di Cincinnati. In particolare stava già lavorando con Greg Morris, fondatore della Morris Technologies e altre figure di spicco del movimento additive, per la produzione di un fuel nozzle super efficiente destinato a un motore di nuova generazione, il LEAP. “Erano già convinti” dice Abrate, aggiungendo che quando GE acquisì Avio Aero nel 2013 “fummo davvero fortunati, poiché quello accelerò tutto”.
Le pale prodotte a Cameri sono già operative all’interno del motore GE9X, che hanno cominciato a testare all’inizio di quest’anno. Questo motore contiene sia le pale sia i fuel nozzle stampati in 3D a Cincinnati. Faranno sì che questo nuovo motore consumi il 10% in meno del suo predecessore, il GE90. Un grosso vantaggio considerando il peso del costo del carburante per le aerolinee (circa il 19% dei costi operativi).
A Cameri lavorano otto operai specializzati che usano le machine inserendo la polvere, rimuovendola, ripulendo le parti e facendo manutenzione. Ci sono anche nove ingegneri di produzione che studiano le migliori strategie e mettono a punto il processo di produzione. Saranno molto impegnati prossimamente, uno di questi, Dario Mantegazza, dice che “non ci sono limiti alla complessità”.