Invent
Blade Runners
Take a look inside this factory 3D printing jet engine parts.
Oct 2017
Located near the edge of the fertile Po Valley in northern Italy, the town of Cameri could easily be mistaken for a quiet farming commune. But take a short ride through the green, rolling fields around it and you’ll discover a startling contrast.
Cameri, a town of 11,000 people, is the home of the only final assembly plant outside the United States for Lockheed Martin’s F-35B Joint Strike Fighter, a stealthy jet that can take off and land vertically. And just across from the plant’s runway stands another futuristic manufacturing gem: Avio Aero’s 3D-printing factory, making sleek turbine blades for the GE9X, the world’s largest jet engine, which GE Aviation is developing for Boeing’s next-generation 777X planes. The blades spin 2,500 times per minute inside the jet engine, facing heat as well as titanic forces. “These are big blades,” says Giorgio Abrate, general manager for engineering at Avio Aero. “We ran a lot of experiments to get the job right.”
A blue and gray jewel box of steel and glass, the plant holds 20 black, wardrobe-sized 3D printers, made by Arcam. A single machine can print at same time six turbine blades that are each 40 centimeters long directly from a computer file by using a powerful 3-kilowatt electron beam. The beam “grows” the blades by welding together thin layers of titanium aluminide powder, one after another.
Jet engine designers love this strong, heat-resistant wonder material since it is half the weight of the metal alloys typically used in aviation. But it’s also very brittle. Until 3D printing came along, the only way to shape it involved molding, a dirty process that requires expensive tools. “This factory has helped us understand what the art of the possible is with additive manufacturing,” said David Joyce, president and CEO of GE Aviation.
Joyce’s business acquired Avio Aero in 2013. GE also took a majority stake in Arcam last fall, and launched GE Additive, a new business focusing on additive manufacturing technologies like 3D printing. Additive manufacturing is still a young industry, albeit one going through a growth spurt. Mohammad Ehteshami, who runs GE Additive, expects the industry to grow from $7 billion today to $80 billion in a decade.
Avio Aero started exploring 3D printing more than a decade ago. At the time, word got out that GE had used blades from titanium aluminide, known as TiAl, for the first time in the GEnx jet engine it was building for Boeing’s Dreamliner. “For us to step up and bet the engine on this technology is a big deal,” Robert Schafrik, then GE Aviation’s materials and process engineering general manager, told FlightGlobal. “If it has only 50 percent of the weight of the nickel alloys you’ve got to believe this is here to stay.”
The blades GE was using were cast in a foundry. But Avio Aero, which wanted to capture the new market, bet on 3D printing. “We could see how difficult it was to make these blades,” Abrate says. “But we had positive experiences with 3D printing on a military project.”
The company decided to ride the coattails of the nearby Joint Strike Fighter assembly line and set up its additive manufacturing shop in Cameri. “The location was part of our strategy,” Abrate says. “The Lockheed plant made the town become very visible among aerospace companies. We wanted to promote 3D printing to potential customers and they were all coming here.”
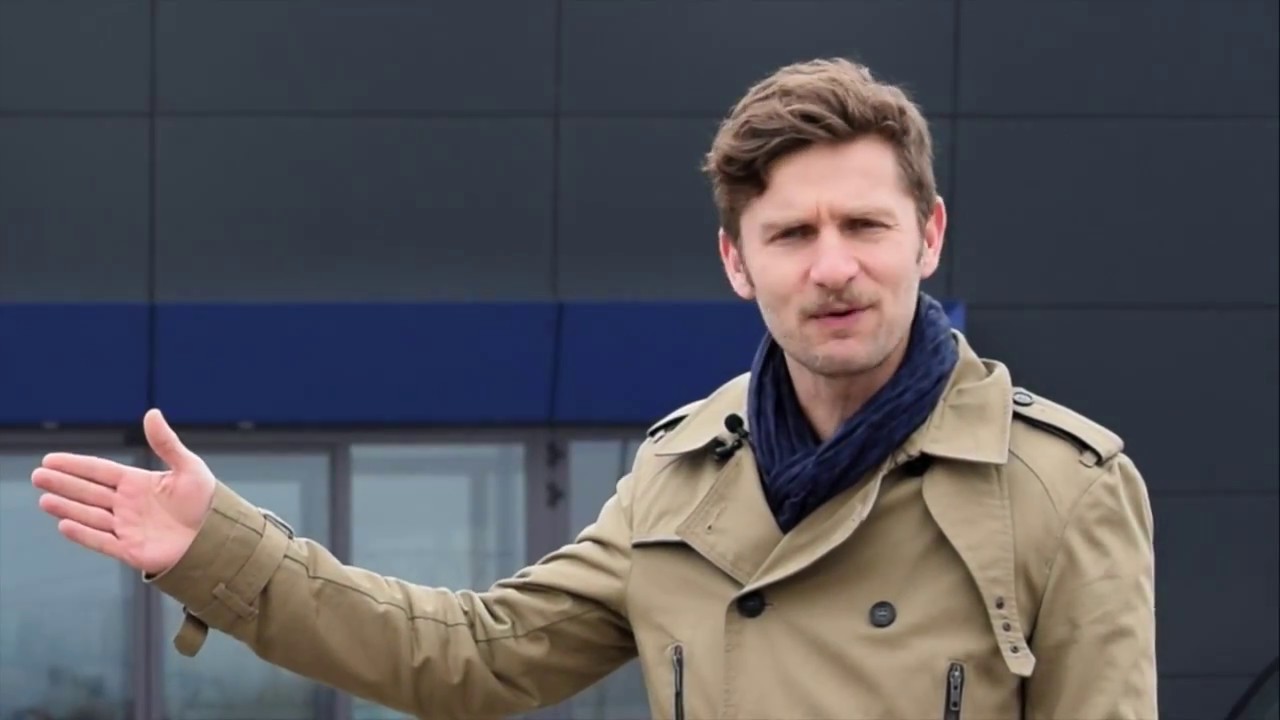
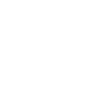
That gamble required 3D printers, which Avio Aero accessed at ProtoCast, an Italian 3D-printing pioneer based in a small workshop nearby. “It was really a garage,” Abrate recalls. “We called it ‘the submarine’ because it was so narrow you couldn’t walk past the people working with the machines.”
But early runs with ProtoCast’s laser-powered printers failed. The blades were cracking when Abrate and the team tried to separate them from the platform on which they were printed.
The submarine, however, had a secret weapon: an Arcam printer that could fuse layers of TiAl powder with an electron beam several times as powerful as the lasers used in typical 3D printers. Abrate reached out to Arcam to tweak the machine’s parameters, make the powder layer thicker and speed up the printing process. Running more experiments, Abrate also learned that preheating the powder before melting it with the electron beam removed much of the residual stress from the parts. “At that point, we knew what to do,” Abrate says.
Avio Aero bought ProtoCast and signed an exclusive agreement with Arcam to supply them modified machines that could print from TiAl. In return for exclusivity, Avio Aero promised Arcam it would buy a set number of printers.
When Avio Aero showed GE what it was doing with the wonder metal, the American company quickly grasped the magnitude of the breakthrough. GE Aviation was developing its own 3D printing program near its headquarters in Cincinnati. It was working with Greg Morris, the founder of Morris Technologies and another leading light in the additive movement, on printing a superefficient fuel nozzle for a new jet engine called the LEAP. “They were already convinced,” Abrate says. He say that when GE acquired Avio Aero in 2013, “it was really fortunate because everything accelerated after that.”
The blades from Cameri are already working inside the first GE9X engines, which GE started testing last year. These engines bring the blades together with 3D-printed fuel nozzles developed in Cincinnati. They will help the engine be 10 percent more fuel-efficient than its predecessor, the GE90. That’s a big deal given that fuel accounts for about 19 percent of an airline’s operating costs.
The Cameri plant employs eight specialized hourly workers feeding the machines with powder, removing and cleaning the printing parts, and doing maintenance. There are also nine manufacturing engineers, who select the production strategy for new parts and tweak the production process. They expect to stay busy. Says one engineer, Dario Mantegazza: “There are no limits to complexity.”