Future
MAESTRO, la lezione continua
A margine della conferenza annuale di Clean Sky 2, il punto su uno dei progetti più avanzati e ambiziosi che già a breve porterà in volo alcuni risultati e che promette nuovi sviluppi.
May 2019
Quasi due anni fa su about, parlammo di MAESTRO proprio in diretta dallo stand Clean Sky 2 - JU durante il salone internazionale di Le Bourget. All’interno di questo progetto, che nasce per il settore dei piccoli aerei per trasporto privato (Small Air Transport), si sviluppano tecnologie per motori turboelica volte a migliorarne i consumi, le emissioni di rumore (il cosiddetto noise footprint), e il costo del futuro prodotto.
Già a quel tempo, MAESTRO si concentrava su tecnologie di additive manufacturing per un componente motore cruciale come il combustore e si presentava come uno dei più importanti programmi di sviluppo tecnologico della partnership pubblico-privata europea che da oltre dieci anni sta tracciando la rotta per un’aviazione futura più eco-compatibile.
Dal 2017, MAESTRO ha mosso importanti passi in avanti e le tecnologie sviluppate al suo interno sono diventate realtà meccanica e operativa per motori turboelica, ad esempio, che voleranno a breve. Infatti, una delle leve tecnologiche più innovative di MAESTRO, proprio quella che si basa sul rivoluzionario processo di produzione tramite stampa 3D metallica, ha già trovato la sua prima applicazione su parti disegnate appositamente in additive manufacturing per il motore Catalyst, cioè gli swirlers del combustore.
“L’Additive Manufacturing più che una soluzione finale è un abilitatore, poiché, in alcuni casi, permette di avere configurazioni più compatte e funzionali a livello di sistema, riducendo il numero di parti, il peso e gli ingombri”.
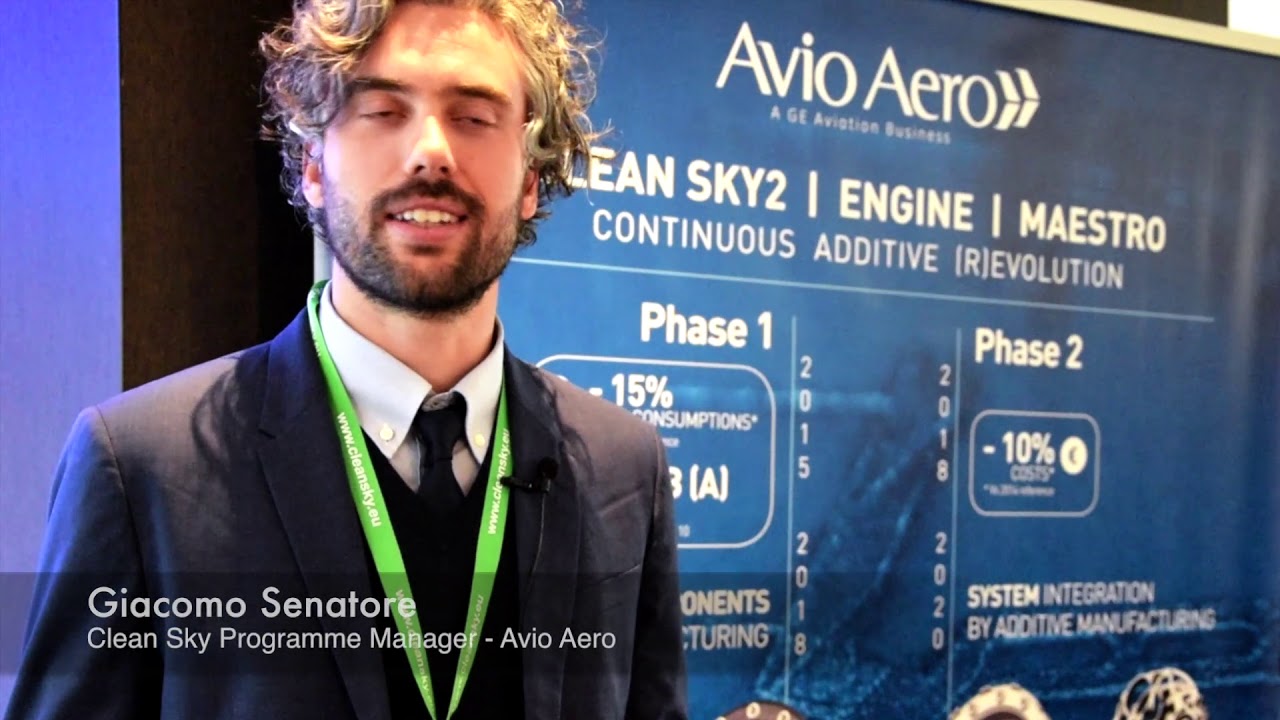
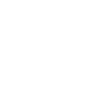
Dicendo questo, Giacomo Senatore, Clean Sky Programme Manager di Avio Aero, si riferisce alla capacità rivoluzionaria della tecnologia additive sia per il design di parti di motore con geometrie piuttosto complesse, sia relativamente al vero e proprio processo produttivo che supera la tradizionale saldatura e manifattura per i prodotti metallici. Virando quindi verso la più silenziosa e precisa fusione di polvere metallica per mezzo di laser o fascio d’elettroni.
Questa è la chiave di volta del progetto, la sua evoluzione che col tempo ne aumenta le ambizioni. “Gli insegnamenti di MAESTRO aprono a nuovi stimolanti scenari”. Aggiunge Senatore. “Si è partiti dal combustore, ma si sta lavorando su altri moduli e componenti complessi”. E allo stesso tempo, nessuno degli ingegneri impegnati in MAESTRO si sente di escludere la possibilità futura di dedicarsi ad un altro segmento di propulsori, non solo i motori turboelica.
“Il combustore ultra compatto con tecnologia reverse flow e con swirlers in additive è senza dubbio un progresso enorme per il settore, ma non esaurisce la parabola evolutiva sia per le tecnologie sia per i prodotti” spiega Antonio Peschiulli, Combustor Design Manager di Avio Aero. “Per quanto riguarda il solo modulo combustore, i nostri studi si concentrano su aspetti altamente d’impatto quali le emissioni e le performance: la temperatura di funzionamento per il combustore è sicuramente una sfida per l’operatività del motore, come per i materiali o per il processo con cui questo può essere costruito”.
"Parallelamente al design for additive, che si traduce in un processo produttivo e prototipale più rapido e pulito, è fondamentale studiare i materiali e le loro resistenze per costruire prodotti più sostenibili"
L’aumento della temperatura è direttamente proporzionale alla produzione di energia, ovvero alla potenza del motore, ma è necessario gestire tale incremento termico dall’interno del modulo combustore in modo da compensare gli effetti delle maggiori temperature sulle parti metalliche e la produzione di emissioni alle diverse condizioni di funzionamento motore.
"L’additive ci permette di immaginare la geometria di un componente partendo da zero, di dargli nuova forma, ma accanto a questo esercizio di progettazione che si traduce in un processo produttivo e prototipale più rapido e pulito, è fondamentale studiare i materiali e le loro resistenze per costruire prodotti più sostenibili" conclude Peschiulli. “Di recente stiamo lavorando a un’ulteriore evoluzione della tecnologia per il modulo combustore, l’abbiamo chiamata Additive Combustor”.
In sintesi, l’additive migliora il design, ovvero forma e peso di componenti o sistemi di raffreddamento motore, e riduce costi e inquinamento del processo industriale tradizionale, migliorando anche le performance con un minor consumo di carburante. L’additive quindi influisce sulle emissioni lineari (che comprendono CO2) legate al consumo di carburante grazie al minor peso che conferisce agli oggetti integrati in un motore che vola.
Infine, il networking gioca un ruolo essenziale dallo sviluppo all’applicazione di tecnologie futuristiche. Avio Aero coordina i team di GE Aviation, membri di quella Federated Europe Engineering che scambia competenze e conoscenze specie su certi programmi di livello Europeo: perciò gli inglesi di Dowty Propellers lavorano alle tecnologie per riduzione rumori, l’Aviation Advanced Technolgy di Monaco di Baviera si occupa del compressore ad alto rapporto di pressione, l’EDC di Varsavia e GE Aviation Czech contribuisce come Headquarters europeo di GE per i turboelica.
“A proposito di networking, il supporto di centri di ricerca e Università, specie in fase di testing oltre che per il contributo talentuoso durante le fasi di sviluppo, è importantissimo”, spiega Enrico Casale, New Technology Introduction Portfolio Manager per Avio Aero.
“Per MAESTRO, ad esempio, ha contribuito molto il nostro Turin Additive Lab all’interno del Politecnico di Torino, che sta inoltre diventando sempre più un luogo dove non solo si prototipa in tempi rapidi e si porta a maturazione il processo produttivo additive, grazie alla presenza di macchine sia DMLM che EBM; ma oggi il TAL è anche diventato un sito certificato per stampare in 3D componenti che possano essere montate su motori destinati a volare. Una collaborazione virtuosa tra industria ed università”.