Invent
Additive contro i FOD
A pochissimo dall’apertura del secondo polo industriale additive, una nuova modalità di cooperazione tra ingegneria e produzione ha già preso una forma accattivante.
Oct 2018
“Il modello instaurato da Avio Aero, fatto di ricerca sull’additive manufacturing all’interno di laboratori - anche con poco più di un anno di vita come il TAL - e prodotti in sviluppo avviati verso la produzione tramite stampa 3D, è straordinario. E per di più, diventa stimolante per qualunque progettista o ingegnere di produzione entrare in un’organizzazione del genere”.
Con queste parole Eric Gatlin, nell’ultima tappa della sua visita agli stabilimenti italiani di Avio Aero, riassume il suo viaggio da Brindisi a Cameri, passando per il Turin Additive Lab. Gatlin è l’Additive General Manager di GE Aviation: è a lui e al suo team che compete guidare, connettere e supportare in ogni parte del mondo le fabbriche di GE Aviation che producono tramite tecnologia additive, o che intendono farlo.
“Nei miei primi sei mesi in questo ruolo, ci concentrammo sul comprendere altre parti di motore aeronautico nei processi di produzione tramite stampa 3D, partendo dai nozzle del LEAP e dalle pale del GE9X, e andando oltre il GE Catalyst” racconta Gatlin, affermando che oggi sono più di 100 in totale le parti fatte in additive su motori GE.
Gatlin è in GE Aviation da tre anni, proviene dal mondo dell’automotive: la sua formazione di ingegnere elettrico, infatti, gli ha permesso di avviare venti anni fa una carriera come progettista di elettronica e sistemi di sicurezza per veicoli, per poi passare alla pura filiera produttiva. Gatlin ha trasversalmente lavorato in tutte le aree della Supply Chain per circa dieci anni, e poco più di tre anni fa entrò in Business & General Aviation, la divisione di GE Aviation che si occupa di motori per aerei a corto raggio tra cui il GE Catalyst.
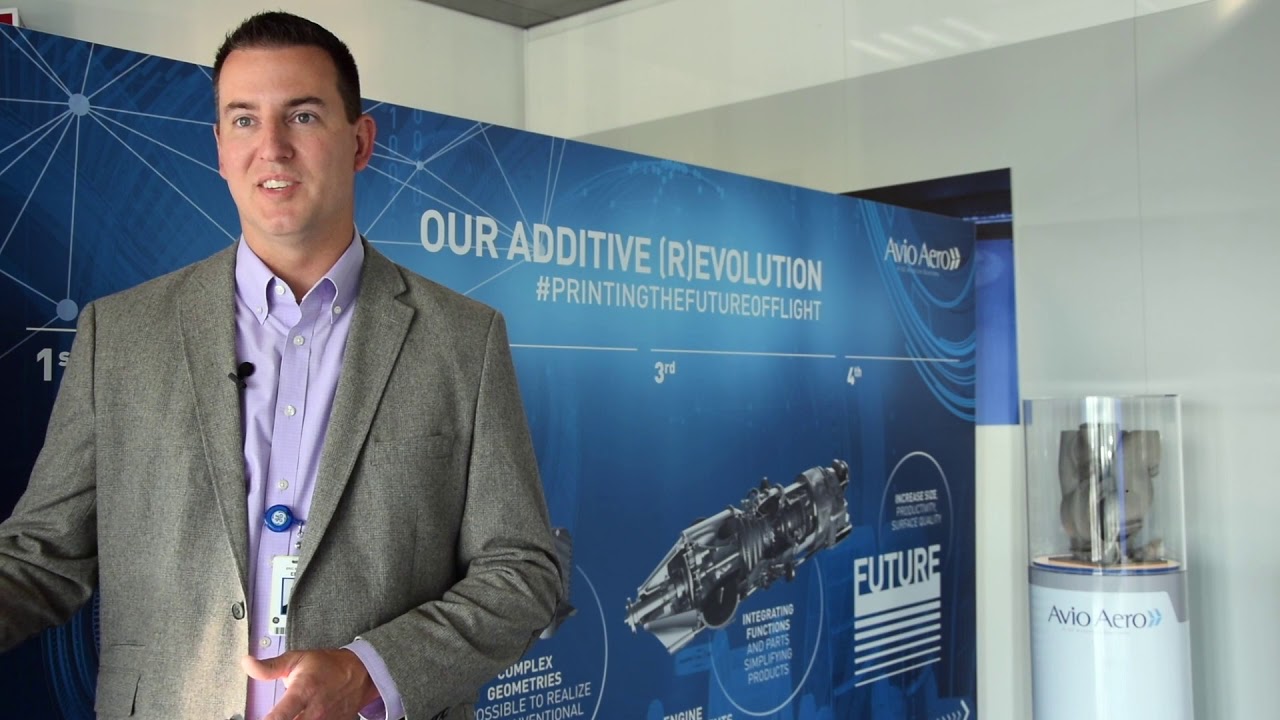
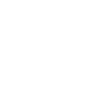
Il suo primo contatto con il mondo additive avvenne proprio a quei tempi, durante la visita all’Additive Technology Center di Cincinnati. “Rimasi talmente impressionato che uscendo da lì dissi al mio capo: se ci fosse mai un’opportunità per me in questa area, ti prego di considerarmi”. La stessa sensazione, l’ha provata visitando Brindisi, o almeno così pare: “Brindisi è un gioiello, vedere ciò che hai discusso e immaginato tra disegni e planimetrie per mesi diventare pian piano realtà in un cantiere in continua evoluzione è magnifico. E poi l’apparato digitale che questo stabilimento già possiede in diverse linee è notevole.”
Il team di Brindisi ha incontrato Eric Gatlin, e quest’ultimo ha riferito di un team decisamente motivato e pronto per tagliare il nastro e cominciare a lavorare in una delle fabbriche del futuro che già dagli inizi del 2019 produrrà una dozzina di parti per il GE Catalyst.
E il team in questione, grazie alla tecnologia additive, gode oggi di un netto vantaggio in termini industriali, una forma di contaminazione tecnica tra figure professionali diverse che promette di rendere ancora più efficiente il motore del nuovo aereo a corto raggio Cessna Denali di Textron Aviation. Si è detto sin dallo sviluppo del Catalyst, infatti, che l’additive ha permesso di ridurre circa 855 parti del motore a sole 12 grazie all’uso della stampa 3D, ma il team brindisino ha aggiunto un’ulteriore riduzione, su un componente che assolve un compito fondamentale. Lo scambiatore di calore aria-olio, ACOC (Air Cooled Oil Cooler), ovvero uno dei tre scambiatori presenti sul GE Catalyst.
L’ACOC è fondamentale perché serve a raffreddare il motore: vicino alla prua del nuovo aereo di Textron, sotto all’elica del motore, c’è una presa d’aria (tecnicamente dett naca scoop) che convoglia l’aria verso l’ACOC che si trova all’interno, sulla parte anteriore del motore, poco distante dalle prese d’aria. Davide Losapio è il designer dell’Apulia Engineering Centre di Avio Aero che ha progettato la nuova forma di questo componente, e lo ha anche semplificato. L’ACOC del Catalyst finora era composto da due parti: quella principale stampata in 3D, e lo schermo protettivo che svolge il cruciale compito di evitare l’impatto con oggetti o corpi esterni (i cosiddetti FOD, foreign objects damage, spauracchio dei professionisti di fabbrica) che potrebbero infilarsi nella presa d’aria. Una soluzione inoltre richiesta dalla stessa Textron. L’ACOC al momento è prodotto da ATC in USA, ma una volta superate le fasi di validazione e certificazione, entrerà nel catalogo produttivo della nuova area additive salentina.
La contaminazione, partendo dal tema FOD, è riuscita attraverso lo scambio di conoscenze ed esperienze tra il progettista Losapio e Paolo Volpe, Additive Manufacturing Engineer di Brindisi, fin dalle fasi di ri-disegno del componente. La magia dell’additive permette anche questo: è tanto veloce la capacità di prototipazione, di realizzazione in macchina e il passaggio dal disegno all’oggetto reale, che il connubio del design con i requisiti di produzione viene quasi naturale.
Per questo, il sito di Brindisi sta arricchendo l’organico con figure professionali che hanno familiarità con la stampa 3D metallica, e nello specifico, che elevano il tasso tecnologico del sud Italia. Paolo Volpe, napoletano 31 anni, è infatti da pochi mesi a Brindisi. “Dopo la laurea in ingegneria aerospaziale, ho maturato esperienze significative in piccole-medie imprese che adottavano processi industriali avanzati. Dapprima come progettista di componenti meccanici realizzati tramite tecnologia Direct Metal Laser Melting (la stessa che usano le macchine di GE Additive in arrivo a Brindisi) per un’azienda all’interno del Centro Italiano Ricerche Aerospaziali, e successivamente come Metal Additive Production Manager in un’altra azienda di Pomigliano che si occupa di 3d printing a 360°”
Per Losapio invece, questa è stata la prima vera esperienza di design for additive. “Ho cominciato a lavorare nel Centro di Eccellenza Frames & Cases brindisino come Tecnologo per i casing delle turbine di bassa pressione di LEAP e GE9X. In realtà, conclusi la mia laurea in ingegneria meccanica con una tesi proprio sul Design for Additive, insieme alla Cranfield University (Regno Unito). E poi ho cominciato come progettista nel team dell’Apulia Engineering Centre che opera tra Bari e Brindisi”.
L’additive non solo ci ha fatto ripensare alla forma, alla geometria dei prodotti sin dal disegno, ma ci ha concesso l’introduzione di materiali assolutamente più performanti sotto diversi punti di vista.
Antonio Gaglianello è il leader proprio di quest’ultimo team, che volge un duplice ruolo: offre l’ingegneria dei motori principali che da sempre vengono revisionati e riparati a Brindisi, e supporta anche progettazione e sviluppo dei cosiddetti NPI (New Product Introduction), e il Catalyst rientra certamente nella categoria. “Questa parte del nostro lavoro ci permette di ripensare completamente i prodotti grazie all’additive”, spiega Gaglianello che, con una decennale esperienza nella progettazione aeronautica, non nasconde l’entusiasmo per la nuova tecnologia. “Se prendiamo ad esempio l’housing (l’involucro, ndr.) della trasmissione di potenza del Catalyst, questa può essere prodotta tramite una tradizionale fusione di magnesio o alluminio. L’additive non solo ci ha fatto ripensare alla sua forma, alla geometria del prodotto sin dal disegno, ma ci ha concesso l’introduzione di materiali, come leghe di nichel, assolutamente più performanti sotto diversi punti di vista, come il peso finale e durezza. Per me, questo è l’esempio tipico di superamento dei limiti dell’industria tradizionale.”
Da un’originale forma regolare, geometricamente rigida, prodotta attraverso brasatura, oggi l’ACOC assume una forma accattivante, la sua superficie è ondulata a verso alternato, è può essere prodotto all’interno di una sola macchina con un raggio laser che in pochi minuti fonde e unisce polvere metallica. “Brindisi sarà uno dei siti produttivi di Aviation più ricchi dal punto di vista tecnico: a partire dalla dimensione della parti, che siano piccolo o medio-grandi, a tutta una serie di nuove polveri metalliche che verranno utilizzate” diceva Eric Gatlin. Se solo la visita all’area che tra poco aprirà ha prodotto in lui certe sensazioni, non vediamo l’ora di varcare le porte del secondo polo produttivo di Avio Aero per l’additive manufacturing per vedere il futuro.
Cessna Denali images credits: Tomas Kellner - GE Reports