Aviation
Colossi marini
Nei luoghi dove nascono le più imponenti navi militari, tra cui la prima PPA di Fincantieri spinta dalle turbine a gas più potenti.
Jan 2018
In una luminosa mattina di dicembre la riviera ligure di levante fa uno strano effetto: entusiasmano al solito i vivaci colori marittimi e i piccoli borghi curati nel dettaglio, ma l’atmosfera rilassatamente ovattata e l’assenza di qualsiasi traffico stonano con la tipica idea estiva che si ha di questi luoghi. È proprio nel tratto di costa che si estende tra due delle mete culto della dolce vita, Portofino e Le Cinque Terre, che non ci si aspetterebbe di trovare, nascosti tra le alture che dall’Appennino ligure si bagnano nel Mediterraneo, due tra i più grandi cantieri navali d’Italia.
A Riva Trigoso (frazione di Sestri Levante) e Muggiano (La Spezia) si trovano i due principali stabilimenti dedicati alla produzione di navi militari di Fincantieri, la cui Divisione Militare ha sede nella città di Genova. Fincantieri è la più grande industria cantieristica del mondo occidentale, vanta 230 anni di storia ed è presente con 20 cantieri navali nel mondo, di cui 8 in Italia dove ha sede l’headquarter triestino. Impiega in totale circa ventimila persone nelle sue sedi, e nella sua gamma di prodotti ci sono imbarcazioni che vanno dalle immense navi da crociera, ai mega yacht (da 70 metri in su), ai mezzi di supporto off-shore, fino ai sommergibili e, appunto, alle navi militari.
Da sempre Fincantieri è al fianco della Marina Militare Italiana, per cui ha realizzato e tuttora realizza le più grandi navi della flotta nazionale, così come è anche partner della US Navy e di tante altre marine estere. Solo tre anni dopo le FREMM - le nuove fregate Europee Multi Missione per le marine italiana e francese - è cominciata, lo scorso febbraio, la costruzione del primo nuovo Pattugliatore Polivalente d’altura (PPA).
Alla fine del mese di novembre i tecnici di Avio Aero Brindisi hanno consegnato il primo modulo turbina LM2500+G4 di GE, lo stesso che motorizza proprio le navi FREMM. I PPA commissionati in totale sono sette, la Marina Militare Italiana riceverà la prima unità nel 2021 mentre le successive saranno consegnate negli anni a venire entro il 2026.
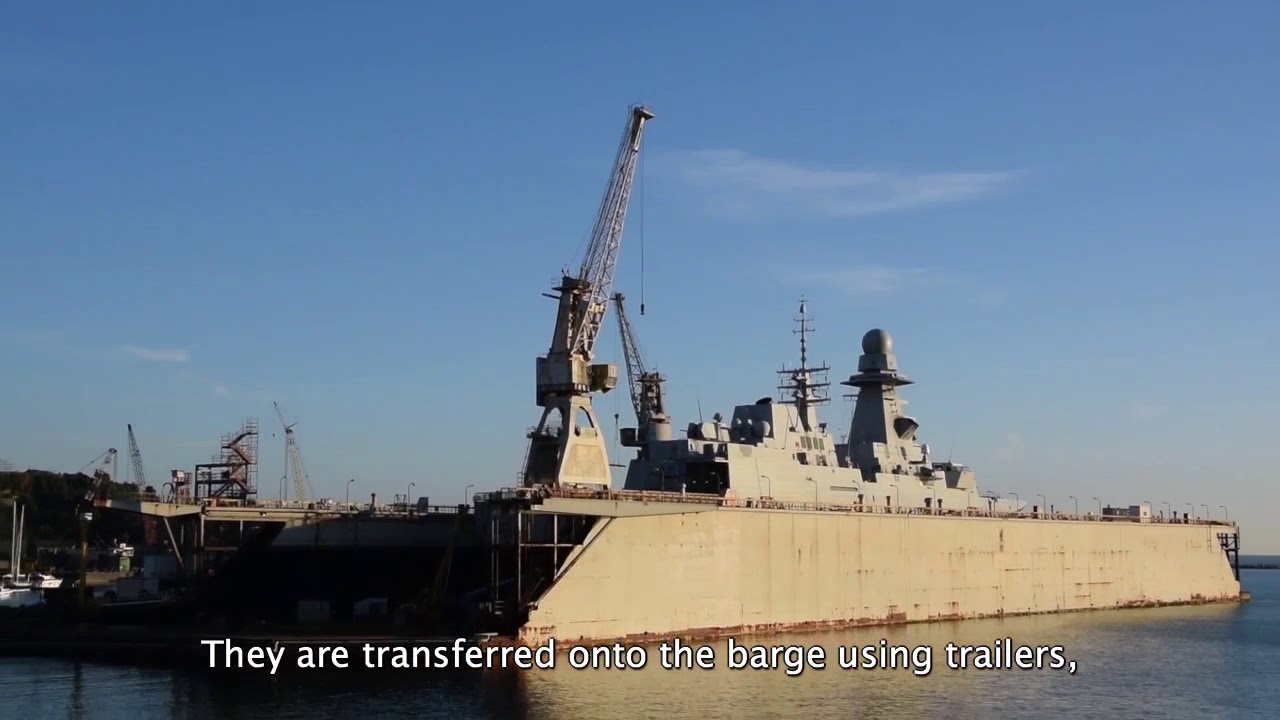
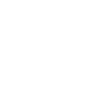
Costruire una nave di 133 metri circa (nel caso della PPA) o persino di 144 metri (la lunghezza delle FREMM, larghe 19,7 metri) può ricordare fantasiosamente quelle costruzioni fatte con il lego: il parallelismo evocativo di giochi di modellismo serve a facilitare la comprensione di un processo di produzione distinto da dimensioni mastodontiche. La primissima fase della costruzione inizia con il taglio della prima lamiera.
“L’oggetto nave è costituito di blocchi che assembliamo secondo un procedimento che parte dal centro della nave e progredisce con la costruzione e il montaggio delle sezioni dello scafo in senso longitudinale e verticale” ci spiega, impegnandosi nella semplificazione, Paola Riva, Direttore della Produzione nel cantiere di Muggiano. In questa piccola località del Golfo dei poeti, hanno costruito parte della prima FREMM (per cui il taglio della prima lamiera è però avvenuto a Riva Trigoso) e cominciato la costruzione della prima PPA. “Riva Trigoso e Muggiano formano, di fatto, un unico cantiere integrato. Infatti al momento a Riva si è partiti con la realizzazione della seconda PPA, la cui prua è in costruzione invece qui a Muggiano e successivamente verrà unita al resto della nave”.
Prima di arrivare a capire come vengono unite due parti di una nave, è utile ripensare ai blocchi che vengono assemblati tra loro in quelle che vengono chiamate sezioni. Ciascun blocco si costruisce tagliando lamiere lunghe 12,5 metri e alte 2,5. Complessivamente un blocco pesa fino a 70 tonnellate, si può movimentare e posizionare per l’assemblaggio dello scafo e della struttura esterna della nave in verticale od orizzontale grazie all’uso di gru. Nel cantiere di Muggiano, quando usate in coppia a causa del peso man mano crescente dei blocchi in costruzione, le gru arrivano a sollevare 140 tonnellate.
“I blocchi con cui si costruisce lo scafo sono poi allestiti nelle successive fasi della produzione” continua Paola Riva “vuol dire che vengono installati tutti gli apparati interni: tubi, cavi, basamenti, macchinari, moduli (tra cui quello propulsivo) e infine arredamenti. Viene completata una struttura che permette di ospitare circa 170 persone, capace di generare energia elettrica e di viaggiare per mare”. Ci sono poi delle strutture impressionanti, le chiatte e i bacini galleggianti.
La chiatta è una piattaforma galleggiante che può essere rimorchiata per mare. Sulla chiatta (tramite dei carrelli) viene trasferita la nave, o parti di essa, per poi spostarla eventualmente o anche unirla al resto di una nave in costruzione. Spostamenti relativamente brevi, pensando ai due cantieri su questo tratto di costa ligure, ma chi lavora in Fincantieri racconta di trasferimenti su chiatte rimorchiate per centinaia di miglia nautiche: da Muggiano a Castellamare di Stabia (Napoli), per esempio.
Sul bacino galleggiante, invece, avviene il varo della nave (che viene spostata qui sopra dalla chiatta): il bacino viene allagato e la nave messa in mare. Dopo il varo si completa l’allestimento in mare con la nave ormeggiata alla banchina per i collaudi e le prove in mare, infine si consegna al cliente. Il bacino galleggiante serve anche per mettere a secco la nave durante attività manutentive, ovvero per operare attività di manutenzione sullo scafo.
Con estrema disinvoltura, pur sempre si tratta di edifici galleggianti e naviganti.
L’installazione del modulo turbina è una delle operazioni comprese nella fase di allestimento della nave in costruzione. La turbina a gas LM2500+G4 viene solitamente assemblata nel centro di eccellenza di Brindisi, dove si produce anche circa il 20% dei suoi componenti, poi viene installata dentro il Base & Enclosure: un cabinato, design esclusivo di Avio Aero, progettato per proteggere e adattare la turbina all’interno della sala motori. Infine, viene trasportata al cantiere navale. I tecnici di Avio Aero, come Giuseppe Cosi, che ha installato insieme ad Antonio Rutigliano la prima turbina sulla prima PPA, si occupano anche della vita in servizio della turbina e della sua manutenzione.
“Nella mia carriera ho lavorato su diversi motori aerei militari” dice Giuseppe Cosi, che a Brindisi lavora proprio nel team di Service. “Negli ultimi anni mi sono occupato di queste turbine a gas e principalmente dell’ambito navale: sono potenti e forse è anche particolarmente stimolante dedicarsi a questo tipo di motori. Gli interventi possono durare una settimana come mesi.”
La turbina LM2500+G4 sviluppa infatti una potenza massima di 35MW, capace di spingere la PPA a oltre 30 nodi (quasi 60Km/h) in combinazione con il resto dell’apparato motore, che comprende inoltre due propulsori diesel da 10MW e due motori elettrici alimentati dai quattro generatori che forniscono energia anche alle altre utenze di bordo.
Il “pacchetto propulsivo” è il cuore delle competenze di Avio Aero sin dai tempi della prima collaborazione con Fincantieri per le navi classe Lupo e Maestrale. “Quella installata sulla PPA è una turbina evoluta che oggi ci permette di andare incontro alle esigenze dei nostri clienti per quanto riguarda le elevate prestazioni di queste navi. Predisporre un prodotto efficace e affidabile, oltre che marinizzato, è la chiave del successo già durante la fase di concept design, fase che vede altresì il lavoro congiunto dei nostri team” racconta Enrico Ferrari, Responsabile della Progettazione dell’Apparato Motore ed Impianti Ausiliari per la Divisione Navi Militari.
Prima del lavoro produttivo, che per completare una nave di queste misure richiede dai 22 ai 24 mesi, esiste un cruciale lavoro progettuale. In Fincantieri la progettazione è suddivisa in: progettazione di base, di concetto e sviluppo del prodotto. Il concept design generale, che recepisce le principali necessità del cliente, è un lavoro talmente nevralgico che complessivamente richiede molto più tempo della produzione. Si misura in anni talvolta.
LA PPA, inoltre, porta con sé un primato raggiunto proprio grazie alla partnership tra l’industria navale e Avio Aero: “la realizzazione del modulo turbina è avvenuta congiuntamente infatti” spiega Pierpaolo Berardi, Program Manager di Avio Aero, che si è occupato della collaborazione nella fase di consegna primo modulo. “Abbiamo lavorato con gli ingegneri di Fincantieri, scambiato competenze e formato anche il personale su specifici aspetti” conclude Pierpaolo.
Esperienza unica confermata anche dalle parole del Propulsion Module Project Engineer di Fincantieri, Alessandro Trucco: “questa collaborazione inedita ha sicuramente rafforzato il nostro rapporto, per la prima volta abbiamo realizzato internamente, attraverso la nostra Direzione Sistemi e Componenti Meccanici, l’assemblaggio del modulo turbina”. Infatti, collaborando con l’ingegneria Avio Aero, Fincantieri ha approvvigionato tutti i componenti del sistema propulsivo, sviluppato le istruzioni di montaggio interne e fisicamente assemblato i componenti del modulo turbina. “Abbiamo compreso meglio funzionamento e caratteristiche dei componenti della turbina, acquisito know-how per l’integrazione di un modulo complesso a bordo di una nave: a Riva Trigoso, inoltre, abbiamo allestito una speciale ‘Clean Area’ per il montaggio in casa del modulo. Tutto questo lavoro congiunto certamente ci permetterà di inserire nuove opzioni nelle future proposte ai clienti”.
Pensando alle marine estere che stanno manifestando più di un curioso interesse verso i pattugliatori e le loro soluzioni propulsive, si può dire senza timore che l’avventura per mare a bordo di questi colossi è destinata a raggiungere ancora altre rive, altri contenti.