Invent
Gran Torino
The Sangone Test Center, inside Mirafiori automotive kingdom, inaugurated two new test cells for engine modules powering A400M and the new Denali.
Apr 2018
In 1950s, when Turin was right in the middle of the Italian economic boom, with Fiat busily producing motor cars in what would be the start of a new transport era, Mirafiori was the industrial town in the city. At that time of extensive building and technological development, Mirafiori was home to the largest industrial area in northern Italy, and it was an ongoing expansion. The south-west borders of this small city within the city of Turin was the Sangone river. Around the same time, among the industrial buildings where car engines and bodies were taking shape, the Avio Aero Test Center was established.
It was in the rooms of the Sangone Test Center that the tests on the last radial engines to fly during World War II took place, as well as the first tests on the new-concept engines of the time: such as the General Electric J79, and eventually the EJ200 and T700 towards the end of the 1980s. Today, in this test center occupied by just over sixty employees, we are witnessing the transformation of some of those historical testing rooms and buildings: just as in 110 years of Avio Aero history the development of aircraft engines has gone through innovative transformations.
“The activities taking place at our center”, explained Michele Fantetti, Engineering Experimental Testing Leader, “are linked to technology validation and certification of the modules which Avio Aero has responsibility for within the NPI programs (New Product Introduction ed.), as well as the NTI programs (New Technology Introduction ed.).” In fact, Fantetti studied locally at the Politecnico di Torino - a breeding ground for engineering talents traditionally attracted by the city’s main industry - where he, however, graduated (with honours) in aerospace engineering, adding to the large group of engineers that have used instead that university as a launching pad for a career in the aviation sector. “In reality, the Sangone center is not just connected to the GE Aviation Testing Engineering Team, but also to its counterparts in Pomigliano, the Flight Test Center in Caselle (Torino), the Labs in Rivalta and PoloniaAero”, explained Fantetti who, in his career at Avio Aero spanning more than fifteen years, has covered roles ranging from turbine and transmission design to engineering responsibilities alongside the Supply Chain and, of course, testing. All in different places, in Italy and in Europe.
Fantetti suggests that this major restructuring of the test cells at Sangone came about in order to embrace product and technology evolution. “It’s a particularly complex restructuring”, added Gennaro Oliva, Industrial Plants & Equipment Risk Officer at Avio Aero. “We started with the complete overhaul of the structure of the cells and the complete reconstruction of the systems, in order to give our colleagues cutting-edge test cells.” Oliva is also a well-known figure within the company: he has been involved in a large number of industrial construction and restructuring projects of varying complexity and geographical location (he has worked in Italy, Poland and China). “We have restructured 1,100sqm for the two new cells at the Sangone center, and built another 300sqm from the ground up in an area where the discharge pipes from the old test cells were located”, he concluded with pride.
The two new cells at Sangone are actually those where, at one time, entire engines were tested, such as the J79 or LM2500, and soon these renovated spaces will house a concentration of pure aeronautical technology: the power transmissions of the TP400 engine for the Airbus A400M and the new GE Catalyst engine, destined for the new Beechcraft Denali.
Many different types of tests will be conducted in the new cells: “It will be possible to assess vibrations, carry out strength tests, tests consisting of the accumulation of cycles usually over 150-300 hours, as well as the application of loads to transmissions to evaluate, develop and improve engine performance, and telemetry tests will also be performed”, Fantetti briefly said, emphasizing the latter. “Telemetry allows us to fit the rotating gears with sensors and to acquire the signal while the component rotates: it’s a giant leap forward, because until now we could only fit them to the static parts of the module. Everything was connected by cables, so if we fitted sensors to the rotating parts the cables would snap...! Now, however, we can monitor dynamic strain and stress right in critical points of the rotating components: between the gear teeth, and in the shafts’, critical areas. Imagine how much more design information we can hand over to our colleagues.”
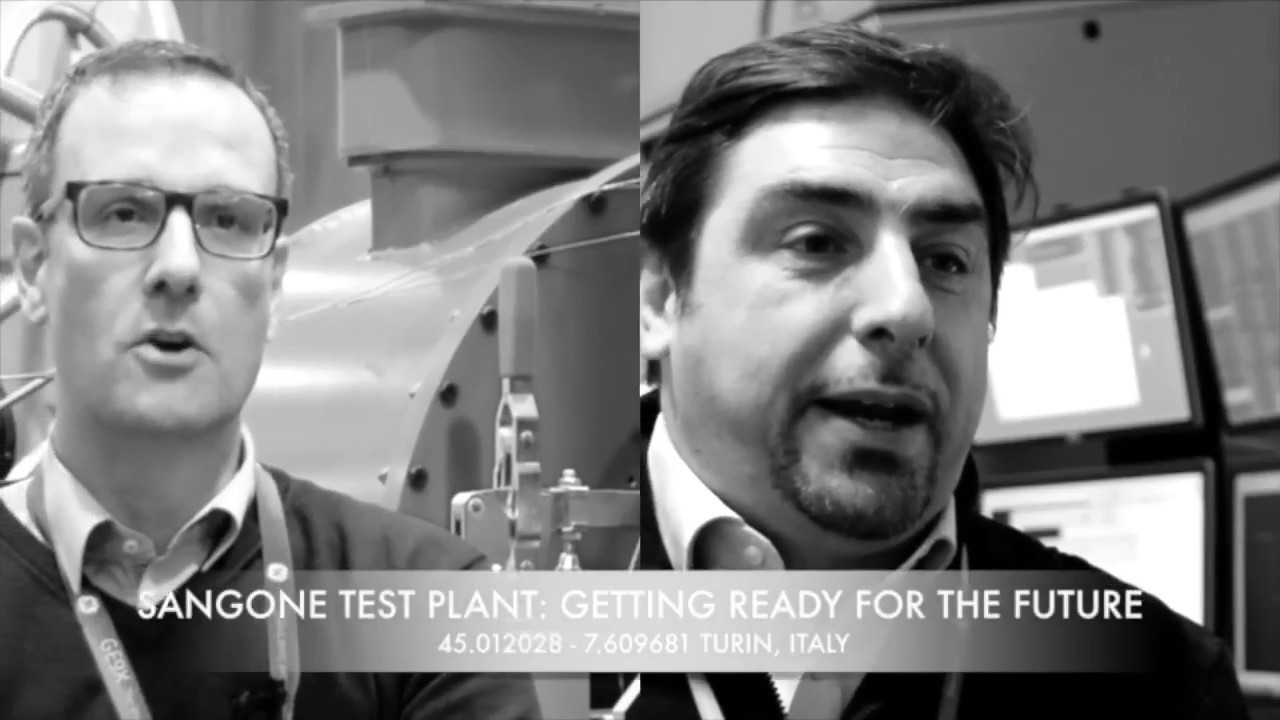
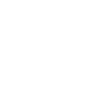
Data, information and acquisitions that need to be shared increasingly quickly and more effectively with the other teams designing components or performing complementary tests for the engine, “internal clients” as Fantetti calls them. “We’ve launched various initiatives in relation to the digitalization of these processes, based on data acquisition, transfer, post-processing and validation. GE Aviation developed, and is still developing, digital tools to help manage an ever increasing amount of data processed through algorithms, therefore requiring an IT infrastructure that automates and standardizes the process for everyone, and also provides the data in real time. We’ll adopt or adapt the most suitable tools for our products.”
The Sangone Experimental Center has been revamped, with these new testing rooms and new products to test. It is changing and transforming, but its DNA still remains the same, with an enduring connection to testing which enables innovative solutions to be found for the engines of the future. And, given the close proximity to the car industry, some day we could even spot a flying car in the skies over Turin.