Invent
Maestro ready for take-off
The European research project for small air transport has contributed new technologies that will soon fly with the Catalyst engine, whilst looking ahead at driving an even more sustainable future.
Aug 2020
In the world of aviation, special skills, advanced technologies and new products can all interweave in an exciting way. A bit like what happened to Lorenzo Fattorini, the young engineer who shared recently how he had joined Avio Aero's Additive Design & Technologies team with a mission to develop solutions for the additive manufacturing of components for new engine programs.
At the time, Fattorini was beginning to explore and apply the unimaginable opportunities that additive manufacturing – or 3D metal printing – can give designers of aeronautical engines in terms of geometric freedom and design flexibility. “The experience gained was crucial to help me grow on a management level, allowing me to gain insights into project management logic within European-funded projects, and also on a technical level, thanks to the work I was able to do on extremely innovative components such as the ACOC (Air Cooled Oil Cooler) for the Racer by Airbus Helicopters.”
Today, Fattorini works full time together with a dozen other Avio Aero engineers - in collaboration with GE Federated Europe Engineering teams from GE Aviation Czech, GE Aviation Company Polska, EDC, Aviation Advanced Technologies (Munich), Dowty Propellers and GE Aviation Systems (Cheltenham, UK) - on the Clean Sky 2 Maestro project. The latter is part of the largest European research program devoted to the decarbonization of aviation and to the most ambitious environmental sustainability objectives: the Maestro project aims to reduce CO2, NOx and also noise emissions for engines in the small transport aircraft segment.
A very simple equation for Avio Aero's engineers: additive manufacturing, high performance and efficiency turboprop engine, reduced fuel consumption and emissions... all this is inside the Catalyst engine. “In this new job, I went from managing a very small technical task to the higher level management of the project as a whole, incorporating some fascinating aspects when it comes to interactions with other major market players and, above all, a much more concrete view of the final application for the technologies studied in the last five years on board the new Catalyst engine.”
Since its launch in 2015, the Maestro project has produced a series of fascinating technological developments for the small air transport segment (one of the categories of aeronautical applications on the long list in Clean Sky 2). First and foremost, the compressor is a component that may be considered as a "flagship of innovation": it allows a ratio of 16:1, meaning that the air entering the engine is compressed up to 16 times at the outlet. "It’s a huge improvement, unparalleled among the turboprop engines currently available in the market and it also guarantees a 7% reduction in total CO2 emissions."
Such technological developments in the compressor and turbine modules - in the latter case, optimizing aerodynamic losses from the connection zone between the high-pressure and low-pressure turbine to the exhaust zone has made it possible to increase propulsion efficiency and at the same time reduce CO2 a further 3% - are effectively an integral (and tangible) part of the avant-garde technological content on board the new Catalyst engine.
“When we started working on the design of a new compressor according to the innovative requirements of the Maestro project (including the new total pressure ratio of 16, previously unheard of in the turboprop segment), we relied on the most modern 3D airfoil shapes similar to those used in commercial long-haul aircraft engines, as well as the inclusion of variable guide vanes”, explains Rudolf Selmeier, Consulting Engineer of the GE Aviation team in Munich. “Later, the complex test campaign on the ACCV (Axial-Centrifugal Compressor Vehicle) conducted together with the Technical University of Munich to validate the aerodynamic and aeromechanical aspects led us straight to the compressor made for the Catalyst. This development activity for a real GE product was a collaboration amongst colleagues from the GE Aviation Company Poland, who were responsible for mechanical design of the compressor as well as aeromechanical design of the bench on which we performed the ACCV tests.”
Fans of the vast aeronautical narrative that in the last five years has marked the major milestones in terms of concept, development and testing of the GE Catalyst, know perfectly well that it is the first turboprop to have several parts made with additive manufacturing, the technological specialty with which Fattorini made his debut in this industry.
“The combustor has seen considerable technical and performance maturity and has been developed to reduce NOx emissions, thanks to the application of 3D printed components such as swirlers”, says Fattorini.
The digital capabilities of the Catalyst - brilliantly contained in its digital brain (the FADEC with integrated propeller control, which allows a jet-like piloting experience) as well as with the one-of-a-kind simulator at Avio Aero in Brindisi – also inspired the digital tool created within the Maestro project and the resulting wealth of data which represents a treasure trove of pure intelligence for the engine.
“Within Maestro, we have also developed internally a software able to predict engine transient performance in the various flight phases”, says Fattorini, “this model has been verified and defined using data from tests on the entire engine performed in the Czech Republic, obtaining really remarkable results on the prediction capacity of the model itself. We were particularly satisfied with the transitional data forecast, the most mutable, fastest and therefore most complex to simulate, obtaining a margin of error close to 2% on average.”
Besides the beneficial effects of such high-level aeronautical research, and its efficient environmental impact on the present small air transport segment, it will be surprising to find out Maestro’s future ambitions (as part of a wider European research that sees Avio Aero committed to electrification of flight). Intensive development work is being conducted with the airframer Piaggio Aerospace aimed at rethinking the engine in the aircraft, with its own instrumentation and equipment: it will be called e-Maestro, providing cleaner thrust for a future turboprop engine and offering lower noise footprint thanks to additional research on low noise propeller blade design with an even more advanced combustor capable of further reducing emissions.
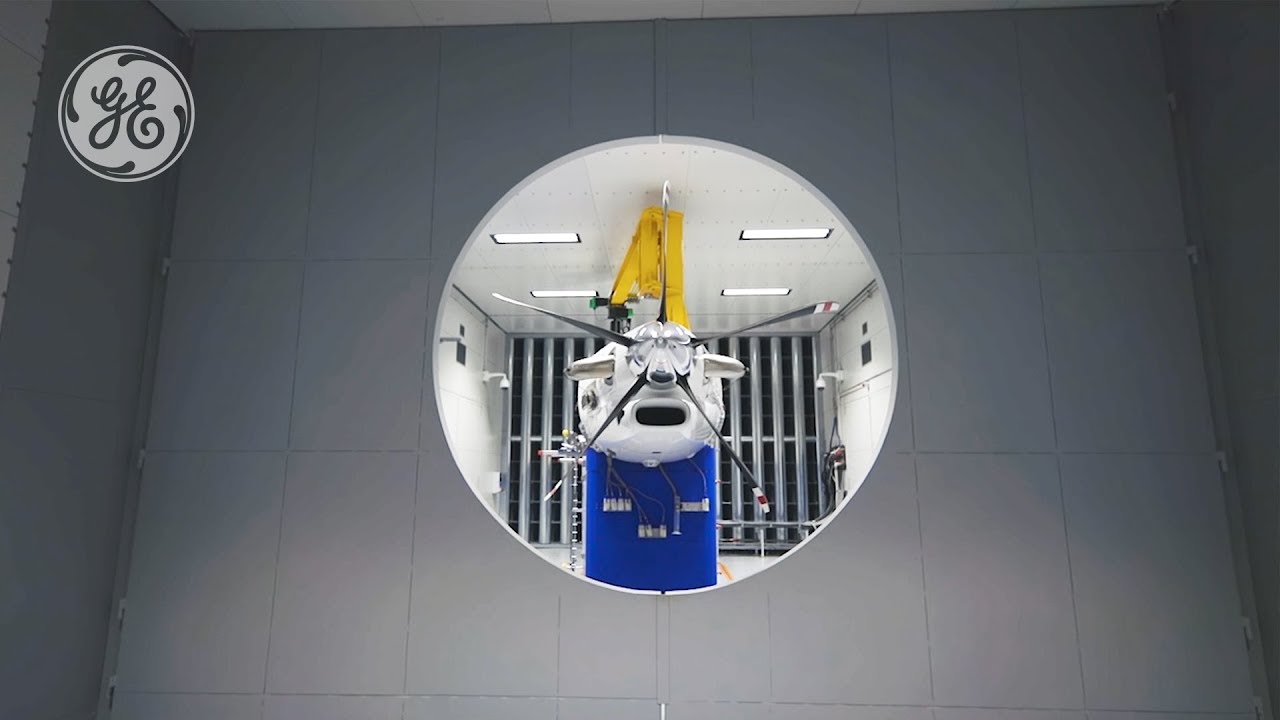
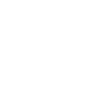
“We immediately saw a great opportunity to conduct in-depth studies of hybrid-electric architectures”, says Fattorini. “First, because we will continue to work on an aircraft and its engine within the same segment, therefore with reduced dimensions, limited power demand and a strengthened technical experience accumulated so far. And because we think this approach eases scalability and so, once progress has been made, these technologies may be transferred to larger aircraft.”
The engineers working on e-Maestro are yet looking for the perfect combination of aircraft and engine architecture that best suits this market sector and allows every engine’s component required to be developed, in order to set solutions that can be applied on aircraft in the real world.
“These initial hybrid studies confirm the design trend towards a distributed propulsion architecture, equipped with multiple propellers to allow optimization of weight/efficiency and reduction of emissions and noise footprint”, concludes Fattorini. “These technological maturations will likely influence hybrid-electric path that Catalyst is autonomously carrying on, just once again in parallel with e-Maestro project. We’ll be able to better understand the potential of sustainability and emissions’ reduction as we go forward with our cooperated work through hybrid architectures in the next months”. And we already see room for more electryfing stories!
Cover image credits: GE Aviazion Czech, CVUT.