Aviation
Cutting-Edge Helicopters
The VRT500 is the stylish, disruptive newcomer onto the lightweight helicopter scene featuring pioneering technologies and Italian excellence, even in its main rotor drive system.
Jul 2021
In a world that is radically transforming the concept of urban mobility - within or between big cities, focusing on safety, agility, connectivity, and sustainability- the new VRT 500 designed by Aeroter is set to be a unique aircraft in terms of innovation, design, and operational flexibility.
The VRT500 is about to enter the lightweight single-engine helicopter market and already boasts two firsts in its class: the larger cabin space and a larger cargo rear door. These records contribute to it being available in eight different configurations: in addition to transporting passengers (up to six), in taxi mode or in the business version, the VRT500 can be used for cargo, training, public safety, and medical or rescue services.
The style and eye-catching appearance exclusively designed by the famous Italian brand Italdesign Giugiaro are a prelude to the advanced technological equipment and avionics on this innovative helicopter. These range from the latest generation control cabin capable of facilitating the pilots’ work through its interconnection with complete electronic monitoring, to the powerful and reliable PW207V turboshaft by Pratt & Whitney that powers the main coaxial rotor with counter-rotating blades (a key, visibly distinctive element on top of this helicopter).
The main transmission system of this jewel of helicopter innovation also comes as the result of the ingenuity of another Italian brand in the aviation world, Avio Aero, which designed it ad hoc and builds it in its new, optimized industrial ecosystem for helicopters at its plant in Rivalta di Torino.
“I joined the VRT program at the end of 2020, learning the operating principles from my colleagues, Gaetano Ghu, who oversaw its industrialization from the initial stages,” says Giovanni Olivieri, New Product Introduction Manager for VRT program at Avio Aero. “The new engineering and industrial approach we developed for our helicopter products has allowed us from the outset to focus heavily on the ‘complexity’ of this specific product. Not only in terms of the general performance of the aircraft, but especially for the level of safety to be ensured.”
The main rotor of the VRT500, at the core of this aircraft’s remarkable performance, is very stable even in strong winds, as well as being highly maneuverable in densely populated areas. With a maximum take-off weight of 1900 kg, the VRT500 has a top speed of 250 km/h (for example, it can connect Rome and Milan in about 2 hours) and a maximum range of 860 km. Given its flexibility of configuration, it aims to play a leading role covering mid-range travel, such as Heli-Taxi activities.
“For Avio Aero, this program is an all-around challenge, since the involvement of the Rivalta headquarters (about 50 people), the Borgaretto specialized centers for the housing, the Sangone plant for testing, and, looking ahead, of the Pomigliano site for service, meaning that we are responsible for both the design of the entire main transmission system with the Engine Oil Cooling System (EOCS) and the industrialization of a highly complex system. For this product, we coordinate the quality and safety of a supply chain spread across the world,” says Gabriele Di Carlo, Lightweight Single-Engine Helicopter Program Manager at Avio Aero.
The product we have built goes through a process that has been studied down to the last detail, in particular the assembly phase, which literally revolves around a transmission shaft of considerable size, up to the final power test performed in a brand-new test cell
The Rotor Drive System of the new VRT500 includes sub-assemblies and parts belonging to legacy technology (i.e. based on established and benchmark products for aeronautics) as well as new content. Industrial coordination and the new integrated process from production to assembly and subsequent testing are therefore crucial.
“The product we have built goes through a process that has been studied down to the last detail,” explains Giovanni Olivieri. “In particular, the assembly phase, which literally revolves around a transmission shaft of considerable size (it is about 1.7 m long), requires such attention to details that we have even performed the final power test in the new test cell in the area dedicated to helicopter transmissions, ensuring our highest quality output.”
Avio Aero's system performs the delicate and essential task of transmitting motion and power from the engine to the two counter-rotating blade rotors of this cutting-edge helicopter. In turn, the transmission system consists of the main gearbox, input shaft, rotor brake and sensors, integrated with the EOCS, which manages the oil cooling for the main gearbox and the engine.
“This innovation also helps us to facilitate customer integration work and collaboration with historical partners, such as Pratt & Whitney,” explains Emanuele Di Leo, Helicopter Transmissions Commercial Manager. “This type of architecture with coaxial counter-rotating coupled rotors, which includes the integrated cooling system for gearbox and engine, is a very exciting innovation for all of us and gives the advantage of a more compact transmission, capable of making the most of the motor’s power while still avoiding a tail rotor. It also gives the aircraft greater in-flight safety, maneuverability, and more transportable load, as well as significantly reduced noise emissions.”
Designing an entire system where there are so many critical components that require ad-hoc design methods, new accessories and functions, as well as playing an active role in the certification, certainly excites us
Avio Aero is set to deliver three complete transmission modules by the end of 2021: “two will be destined for on-ground and development testing; whilst the third will be for the first flight prototype, to achieve the goal of lifting off the ground for the first time by the end of 2021. In 2022, other prototypes are expected to be delivered to support certification campaigns, which we estimate achieving by the end of 2022,” adds Di Carlo.
The motivation and enthusiasm of Avio Aero’s team of professionals and engineers involved in the VRT500 program are palpable. Theirs is a delicate and fundamental role that has led them to form an integral part of the development of a helicopter never built before, right from day one, side by side with the customer.
“Designing an entire system where there are so many critical components that require ad-hoc design methods, new accessories and functions, as well as playing an active role in the certification, certainly excites us,” comments Di Carlo, echoed by Di Leo, who reflects on the unprecedented “architectural” challenge with a customer that is a pioneer in terms of helicopter experience and tradition.

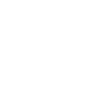
“Counter-rotating rotors intrinsically have a very high mechanical complexity. Two swash plates are required, one for each rotor, capable of differential tilting, with perfect synchronism and mechanical couplings able to provide opposite torques to the two rotors,” concludes Di Leo. “Only very few industries in the world have the necessary know-how to design such complex systems.”
The attention to detail, the curiosity, and the desire to discover and see this new product flying convey a clear awareness that power transmissions are key products for the future technological development of air mobility, for turboprop aircraft as well as for helicopters. It is right based on such technology that Avio Aero is envisioning even the electrification of flight.
VRT500 image and video in page are courtesy of VR-Technologies ©.