Aviation
Bavaria meets Salento
At the Wet Rig in Brindisi, the preliminary integration tests for the GE Catalyst with the propeller made by MT Propeller and dedicated to military applications have been kicked off.
Jan 2020
Arrival on the fly: surely, it is not a figure of speech for Martin Albrecht. The Vice President and General Manager of MT Propeller - the Bavarian company that last summer signed a collaboration agreement with Avio Aero to supply its propellers for the GE Catalyst engine, specifically for military applications - landed his Piper PA-31T1 Cheyenne at Brindisi Salento airport a few days ago, along with his head of Engineering, Josef Eberl, to meet the local team and to continue the discussions that began at the Company's headquarters in Straubing.
Yet caught by his lively curiosity as an aviator and engineer, Albrecht was finally able to see the Wet Rig in Brindisi up close. Using real fluids and components, this rig has been performing tests for the European turboprop engine, GE Catalyst, for a couple of years. Avio Aero engineers, part of the team usually based at the laboratories in Bari, welcomed the two guests and showed them the Brindisi test cell (the only one of its kind), where they’re used to perform the operational part of their job.
In a mix of enthusiastic concentration and desire to go into action with tests, Albrecht and Eberl first were guided by Avio Aero through the screens and diagrams of the control room. Then, the guests entered each of the two chambers that house the real accessory gearbox and the real power transmission. Here, the equipment is operated from the control room using a real throttle and the digital brain of the Catalyst engine (the FADEC with integrated digital propeller control, which is also a key feature of the Wet Rig) to simulate each phase of flight.
"It is an exceptional test environment, here we can simulate the interaction between our propeller and the engine perfectly, particularly in the power transmission chamber. This is the component on which the propeller system is installed," commented Albrecht at the end of his first tour of the Wet Rig. "We will get the dynamic response of propeller-engine integration. The big advantage here is that we can test the behavior of the entire system well before the full engine test in a traditional test cell. We can reliably predict the installation on aircraft."
The traditional engine test with the propeller will most likely be performed in GE Aviation's new high-performance test cells in Prague, but Albrecht's expertise immediately identified the key motive for the Wet Rig tests. They provide an important advantage in terms of time and cost management. In the Brindisi test cell, all the crucial components are present and working exactly as if they were assembled on the engine, as if they were on the runway or yet in flight.
"The big advantage here at the Wet Rig is that we can test the behavior of the entire system well before the usual whole engine test, and even predict the installation on aircraft"
"It is extremely innovative; something we've never done before," continues Albrecht. "We are very optimistic. Once we've calculated the requirements in terms of speed, altitude and installation on the aircraft, we will be able to provide a 5 or even 7-blade propeller that fits perfectly... Efficient, lightweight and low noise."
Already the objective is clear and well defined for both the Avio Aero and MT Propeller teams. The engine and its propeller must be able to reduce emissions and reach high performances as well as altitudes in flight. Therefore, the first test phase will be digital.
The propeller’s specific data will be entered into the FADEC system. This will provide the basis for initiating analysis and possible optimization. The second phase will focus on the real integration of the two products, the engine and the propeller, and everything will take place at the brand-new GE Aviation Czech test cells in Prague.
"The presence of the FADEC with integrated propeller control will allow us to optimize the test phase from both a mechanical and digital standpoint... Here in Brindisi, somehow we will simulate the Catalyst engine as if it has its beautiful MT propeller integrated and mounted," adds Paolo Salvetti, Sales Director for Military Turboprop Engines at Avio Aero, who set up the entire collaboration initiative with Albrecht and bringing it to fruition thanks to the support of the Avio Aero teams involved.
"This will allow us to strongly reduce both risks and integration times on future aircraft applications and therefore to have a proven and ready-to-use engine solution available on the market," says Salvetti in conclusion. In a technologically complex world like aviation and under the unpredictability of skies, this type of opportunity is almost a luxury.
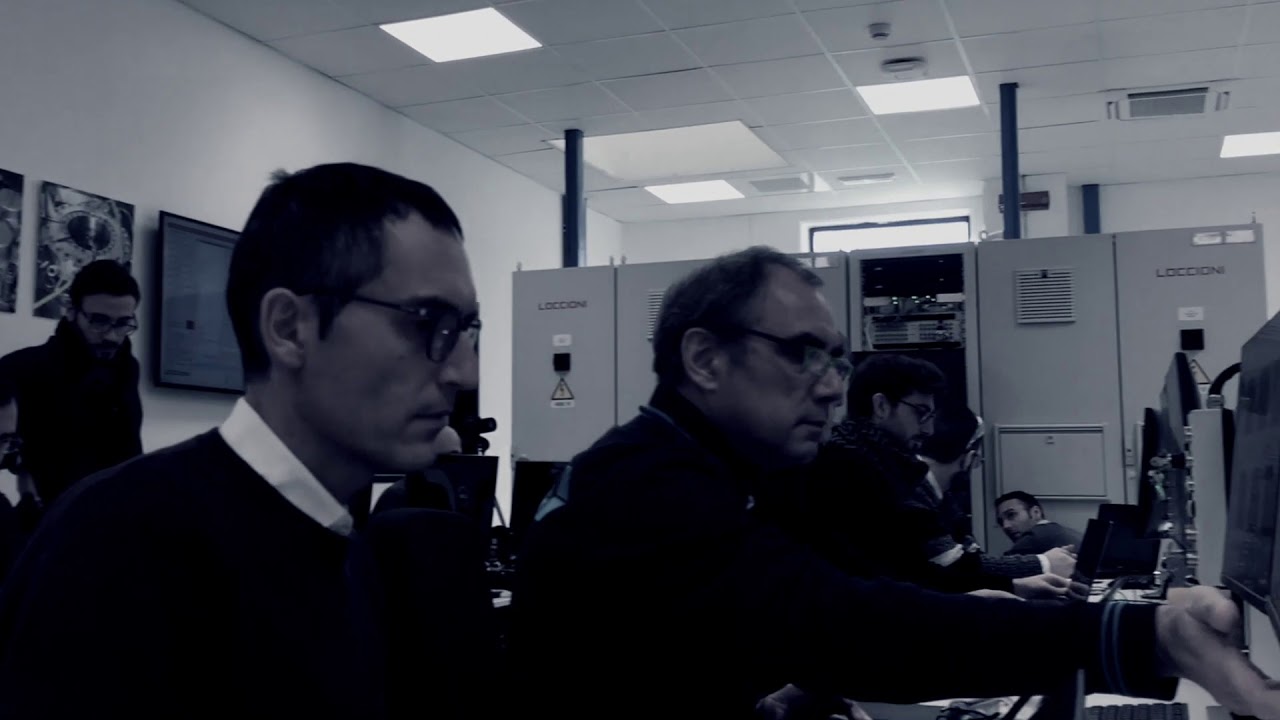
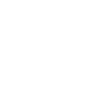